In many industrial applications such as construction machinery or agricultural equipment, hydraulic systems play a significant role. For any other hydraulic component to perform perfectly, Kawasaki hydraulic pumps are among the necessary parts that require maintenance and adjustment on a regular basis. When no measures have been put in place, the issues with the hydraulic pump can lower machine’s performance, increase operational expenses and may even lead to machine downtime. Consequently, effective troubleshooting and adjusting of Kawasaki’s hydraulic pumps becomes highly indispensable in this regard. In this article we provide tips for troubleshooting and adjusting Kawasaki hydraulic pumps so that you can keep your fluid power system functioning effectively.
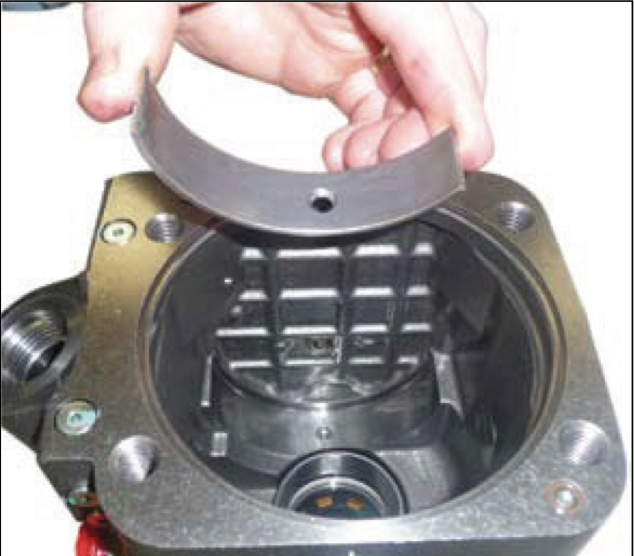
Comprehending Kawasaki Hydraulic Pumps
Kawasaki stands out as a top maker of hydraulic pumps. It supplies a variety of products for different industrial uses. In the industry, Kawasaki hydraulic pumps are recognized for their sturdiness, dependability and great performance.
The structure of Kawasaki hydraulic pumps includes housing, shaft, pistons, swash plate and valve plate. The housing is an outer layer which protects internal parts while the shaft connects the pump to an engine or motor. Pistons create pressure in the system while the swashplate changes piston angle thereby altering the amount of pressure created by them. Valve plates on other hand regulate flow rates or volumes of hydraulic fluid through these pumps.
By this discussion it should be clear that what sets apart kawasaki hydraulic pump from other brands lies mainly on its design simplicity coupled with excellent performance characteristics during high pressure work cycles such as those encountered in construction applications where heavy machinery is used frequently over long periods without interruption because all components necessary for achieving desired results are contained within one single unit thus eliminating need for complex interconnections between separate units each having own reservoirs filled up independently before starting operation so that when compared side-by-side against any other type even if they have same specifications except being made by different manufacturers one can easily realize that this machine offers more advantages over others.
Kawasaki’s hydraulic pumps work by converting mechanical energy into hydraulic power. They take oil from a tank and pressurize it before sending throughout circuitry where required like cylinders or motors etc., in order to perform certain tasks. For instance; lifting heavy loads with arms; rotating drums; moving conveyor belts back forth along specified paths – all these activities can be done only thanks to such devices which transfer forces created by engines into necessary motions using liquid medium thus enabling objects being manipulated electrically controlled machines powered either directly via batteries or indirectly through generators driven by combustion engines running on diesel fuel but always operated remotely without human intervention until complete programmed sequence has been executed successfully after which everything stops working again until next command is given so that amount produced must be adjusted accordingly.
Kawasaki Hydraulic Pump Problems; Signs and Symptoms
Various problems can affect the performance of Kawasaki hydraulic pumps which are vital components in hydraulic systems used in industrial applications. Such issues should be identified early enough for troubleshooting to be done so as to prevent more damages from occurring thereby reducing downtime.
Below are some indicators that a Kawasaki hydraulic pump is problematic:
Low Flow Rate: When the rate at which fluid flows through this device decreases, it slows down operations of other parts connected with it. Several things cause this including wear out of different parts making up the pump itself; clogging filters or leakage within system among others.
Too Much Noise: If an abnormal noise level is detected during its operation then something might not be right somewhere inside it! Cavitation could lead to excessive noise generation together with worn-out bearings or damaged components but even air trapped inside could create such sounds.
Liquid Leakage: One should know when there exists any form of liquid leaking out from anywhere around these machines because that signals trouble too. Seals get old hence become less effective while some parts may have experienced damage leading them into faulty working condition thereby allowing fluids pass through where they shouldn’t.
Overheating: A hydraulic pump gets too hot when operating under high temperatures than what was intended by manufacturer, this is one sign among many others showing that there’s something wrong happening within it. Lubrication provided might not suffice due to blockage caused by dirty filters leading into increased friction between moving parts thus generating heat beyond normal limits required for smooth running; sometimes wear tear also contributes greatly towards overheating problems especially if pressure relief valve fails to close properly after reaching maximum value allowed causing continuous flow without rest.
Vibration Increase: Excessive shaking noticed when using such devices indicates misalignment somewhere along their setup lines or rotating shafts which can easily result in reduced efficiency over time. Again vibrations come about through wear tear on different sections like cylinders and rods but equally unbalanced loads will have similar effect.
Drop in Pressure: Another major issue that should never be ignored has to do with pressure drop recorded during operation. When hydraulic oil fails to reach expected levels within a given system this means there are problems which could be arising from worn out parts or clogged filters among others; leakage may also play role here as well.
Slow Response Time: If response time becomes slower than usual then one need not wait for long before realizing something went wrong somewhere while setting up such equipment. Reducing productivity is always accompanied by increased downtime thus making everything less efficient in general terms. Such slowness arises due to either wear and tear on various components like valves, cylinders etc., clogging of different points within circuits through dirt accumulation over time plus leakage that could occur anywhere along those lines thereby not allowing necessary pressures build up at required instances.
Factors Affecting Adjustment of Kawasaki Hydraulic Pump
Effective adjustment of Kawasaki hydraulic pumps is dependent on a clear understanding of various factors that can influence their efficiency. Here are some factors responsible for affecting adjustment in Kawasaki hydraulic pump.
Viscosity of the hydraulic fluid: The ability to deliver the required amount of fluid by the pump is affected by viscosity. If it is too viscous, the pump will be difficult to operate resulting into its decreased performance.
Operating temperature: Also the temperature under which this type of hydraulic liquid operates also affects its viscosity which in turn greatly influences the performance of the pump. Too high or low temperatures may result in low pump performance.
System pressure: The amount of fluid that can be delivered by a pump depends on how much pressure is applied to a hydraulic system. In case pressure becomes too high, excessive wearing out may occur thus shortening lifespan of the device.
Pump size: There also exists an importance over a pump’s size when it comes to its output. A small-sized one will not deliver enough fluid while an oversized one would be inefficient as well as expensive.
Pump speed: Speed at which a given pump works determines how much liquid it can discharge from itself. Low speed means less than required quantity discharged while high speed causes more tear and wear on such machine.
Pump type: Different pumps have different performance characteristics that affect their adjustability. E.g., vane pumps are best suited for low-pressure duties while piston pumps are optimized for high pressures.
Pump condition: Similarly, this aspect affects how well such systems perform. In case where there exist defects with these devices then they will not deliver appropriate amounts thereby making them fail to attain peak performances.
Proper understanding about these elements helps one effectively tune up Kawasaki hydraulic pumps and optimize their functioning. Consequently this ensures that businesses run their hydraulic systems at full potential thereby minimizing downtime and increasing efficiency for enhanced productivity gains.
Approaches to Modify Kawasaki Hydraulic Pumps
Kawasaki hydraulic pumps are made to work well in different settings this kind of as building, agriculture, and producing. Even so, you can find situations the place these pumps may perhaps require some changes mainly because of difficulties or other variables concerned with their procedure. You will discover distinctive strategies that could be utilized in modifying hydraulic pumps based upon what type it truly is along with the software it’s employed for. We’ll also look at step-by-step processes associated with many methods of adjusting Kawasaki hydraulics too as their execs and disadvantages.
Modifying Pump Command Levers
The most basic way through which a single can modify these types of pumps is by changing their control levers. This distinct technique turns out handy when one must change pressure from the pump. Adjustments entail turning screws on top rated or side areas right up until desired quantities are achieved. Detailed instructions about this technique involve:
Step 1: Locate lever. This really should not be really hard given that levers are usually positioned near valves around exactly where they hook up with other components.
Step 2: Determine screw. You’ll want to glimpse out for screws possibly located within the leading aspect or even somewhere across sides of your mentioned lever.
Step 3: Turning screw makes changes in pump’s pressure. To raise stress, you switch clockwise when anti-clockwise is used for reducing it.
Step 4: Examination After leveler has become transformed according to preferred amounts test irrespective of whether it however works properly or not by attempting various pressures recorded using gauge.
Execs:
- No unique tool is needed throughout adjustment mainly because this method includes common equipment only.• It might be utilized to make small alterations only especially when working with other procedures would establish cumbersome due to restricted time accessible at hand for such responsibilities like during crisis situations.• The simplicity involved tends to make its applicability wide since any person no matter if qualified or not can certainly have an understanding of and utilize them without the need of any difficulties.
Cons:
- May well not fit big changes. At times men and women may be confronted with problems that may phone for significant changes in these units. In such cases then this technique might not be suitable because it only makes small modifications.• It restricts pressure adjustment to at least one path which could bring about some inconveniences especially if there is really need to change downwards rather than upwards only.
- How to Change the Relief Valve
- The relief valve may be adjusted in another way. A hydraulic pump’s pressure is controlled by a relief valve, which redirects extra fluid to the tank. This can increase or decrease pressure of the pump. Below are some steps on how you can adjust Kawasaki hydraulic pumps through this technique:
- Step 1: Find where the relief valve is located. The relief valve is typically situated at one side of a hydraulic pump; it has a hexagonal shape.
- Step 2: Rotate the adjusting screw. Employ an adjustable wrench so that you can turn this screw on your relief valve. By turning it clockwise, you will raise the pressure on the pump while anti-clockwise will lower down its intensity.
- Step 3: Test for pump intensity After having done with adjusting of relief valves try out whether everything is running well with your pumps.Testing p++ressure would require usage of a gauge for measuring this power (which should be in Pascal).
- Pros:
- It enables more accurate adjustments than levers’ control panel adjustment knob.
- Ideal for large-scale adjustments.
- Cons:
- Needs adjustable wrench.
- Requires technical knowledge and experience when adjusting these valves.
ash plate in place. Use a wrench to tighten the bolt holding the swash plate in place.
Increasing or decreasing the flow rate of a pump is dependent on the swash plate angle. The Kawasaki hydraulic pump’s displacement and flow rate are determined by the swash plate angle. Here’s a step-by-step guide for adjusting Kawasaki hydraulic pumps through this method.
Step 1: Find the swash plate. It is situated on the shaft of the pump and secured by a bolt.
Step 2: Loosen the bolt that secures it in position. You’ll need a spanner to do this.
Step 3: Change its angle. A special tool called swash plate angle gauge should be used in changing it to any desired angles.
Step 4: Tighten the bolt securing it in place…
Step 5: Test the pump. Turn on the hydraulic system and test the pump by observing its flow rate.
Step 6: Repeat as necessary. If the desired flow rate is not achieved, repeat steps 2-4 until the correct flow rate is obtained.
Step 7: Secure the swash plate angle. Once the desired flow rate is achieved, use a wrench to securely tighten the bolt holding the swash plate in place.
Following these steps should help you adjust the swash plate angle of a Kawasaki hydraulic pump.
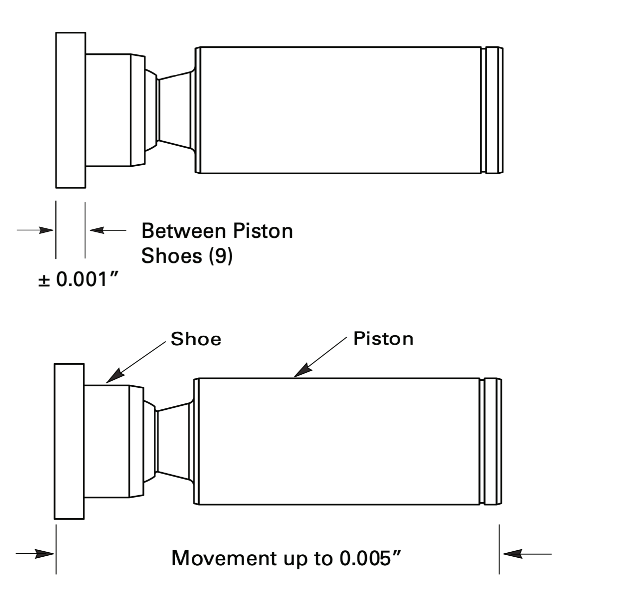
Frequent Errors in Adjusting Kawasaki Hydraulic Pumps
Every process has common mistakes. However, when it comes to adjusting a Kawasaki hydraulic pump, some oversights can reduce the equipment’s efficiency or even lead to its damage. Below are some of the most frequent mistakes that should be avoided during such adjustments:
Setting wrong pressure: The first mistake is setting too high or too low pressure for hydraulic pumps, which could damage them and cause leakage as well as decreased performance.
Failure to follow recommended procedures: Kawasaki gives specific steps for adjusting their hydraulic pumps; thus, failure to comply may result into an incorrect modification that could harm the machine involved.
Neglecting maintenance: Regular maintenance is important if you want your hydraulic pump perform optimally. Ignoring this may expose it to problems like contamination, worn-out parts among others thereby lowering system efficiency.
Using wrong tools: Adjusting tools must be appropriate; otherwise they might spoil everything or give false readings while making these adjustments.
Lack of training: Sometimes people don’t know how to do something correctly because they were not taught so. Similarly, unskilled personnel might not understand what needs doing during adjustment of hydraulic pumps leading to improper settings being made.
Inadequate troubleshooting: It is essential to find out why a particular thing happened before taking any corrective measure on machines. Failure to diagnose the root cause of a problem in a hydraulic system can result into more damages being done through wrong adjustments.
Failure to consider environmental factors: Some factors like temperature, humidity and altitude can affect performance of machines including hydraulics systems. For instance if you fail to take note of these variations while changing settings on such systems then expect incorrect alterations that will lower efficiency levels within them.
Businesses can ensure maximum efficiency from their Kawasaki hydraulic pumps by avoiding these mistakes. Successful adjustment requires correct knowledge coupled with proper training besides following all prescribed methods which go hand in hand with regular servicing based on identified faults during troubleshooting processes among others.
Kawasaki Hydraulic Pump Adjustment Synonyms
Effective adjustment of Kawasaki hydraulic pumps is crucial to maintaining optimal hydraulic system performance. Here are some recommended best practices for a successful Kawasaki hydraulic pump adjustment:
Use the right tools: Before adjusting a Kawasaki hydraulic pump, it’s important to ensure that you have the right tools for the task at hand. Using incorrect tools can damage the pump or system, and also compromise adjustment accuracy. It is key to consult manufacturer instruction manuals and select only prescribed tools.
Adhere to correct procedures: Accurate and effective Kawasaki hydraulic pump adjustment requires following proper adjustment procedures. The particular procedures will depend on the type of pump used as well as the specific required adjustments. Always refer to manufacturers’ instructions and be sure to follow them strictly.
Monitor pressure and flow: In adjusting a Kawasaki hydraulic pump, it is necessary for one to watch both pressure and flow rates. Pressure is related to flow where any change in either quantity directly affects another one too. Monitoring of both ensures that desired system performance levels are being achieved.
Make slow changes: While making changes on a Kawasaki hydraulic pump, one should make gradual adjustments. On this note, if big adjustments are done at once, they may spoil either the pump or even its system too. Instead, little changes should be made while testing each time before proceeding with next step until expected performances are achieved.
Test the system: After a Kawasaki hydraulic pump has been adjusted, it must undergo testing in order to ascertain that intended level of its working capacity has been reached. This may include measuring pressures and flows or running tests under normal operating conditions as well. Regular tests on this device ensure that peak operation continues unhindered.
Scheduled maintenance operations: Proper regular maintenance activities of the whole hydraulic system including synonymous upkeep for Kawasaki Hydraulic Pump helps ensure optimal operational efficiency. Failure to maintain properly could lead issues like leakages or blockage which might necessitate adjustments; similarly such practices could also help extend the system’s useful life.
Education and know-how: Kawasaki Hydraulic Pump adjustment is a task that needs to be done only by professionals having relevant experience. In order to make an effective and accurate adjustment, those responsible for hydraulic pump adjustment must have proper training or be experts in this field.
These tips will help businesses maximize the performance of their Kawasaki hydraulic pumps as well as increase the overall effectiveness of their hydraulic systems.
Conclusion
It is important to know that Kawasaki hydraulic pumps are an integral part of hydraulic systems used in industries. The correct setting of these machines is necessary to achieve maximum efficiency within the system as well as preventing breakdowns which may require expensive repairs and cause downtime. By comprehending the working principles, different elements and functions of Kawasaki Hydraulic Pumps; recognizing problematic indications or symptoms commonly associated with them; plus adopting good adjusting practices alongside maintenance methods – enterprises can greatly enhance their hydraulic systems’ performance while also prolonging its lifetime.
Moreover, companies should invest in training their staff regarding proper adjustment techniques for Kawasaki Hydraulic Pumps so that they can work safely. This will not only ensure that the systems perform better but also create a conducive working environment for all employees. Besides, keeping track on emerging trends in pump technology advancement for future use could enable firms anticipate changes earlier enough thus staying competitive in various sectors of industry.
In general terms, what this means is that if you want your hydraulic system to be optimized then you must adjust Kawasaki pumps properly. Business owners who follow these hints given here will have fully operationalized their hydraulics hence reducing chances of unexpected downtimes or costly repairs.v