It is essential to test a hydraulic pump so that it works well at all times and continues to work well in the future across different scenarios – from motorized machines such as automobiles down to heavy industrial usage. This article will discuss some of the most crucial steps necessary for successfully evaluating how efficient or inefficient a hydraulic pump functions. This knowledge will help readers detect possible problems with their systems by looking at performance indicators like flow rate and pressure levels, among others, thus enabling them to implement appropriate corrective measures. Whether working with fluid power for years or just starting with hydraulics, this manual should offer both breadth and depth needed to improve testing skills while guaranteeing dependability in equipment operation.
What Are the Basic Steps to Test a Hydraulic Pump?
Following several steps when testing a hydraulic pump is essential to ensure accurate assessment and optimal performance. Below are the following steps that can be done according to the current industry standards:
- Preparation: First, you should prepare everything necessary for the test. Make sure that the system has been correctly assembled and that safety measures have been put in place. You will also need different tools, such as flow meters and pressure gauges.
- Visual Inspection: Check for visible signs of wear, leaks, or damage on the pump itself. Also, take time to inspect connections, seals, and hoses for integrity.
- Flow Rate Assessment: This step involves using a flow meter to measure how much fluid comes out per unit time from the output side of your device; it indicates whether or not it delivers expected volumes under various loads.
- Pressure Measurement: Connect a pressure gauge to the discharge line so that you can see what is happening with respect to pressure within this area, vis-a-vis the manufacturer’s rating, which may be written somewhere on its body.
- Efficiency Evaluation: To know this figure, one needs only compare the mechanical input power required by certain hydraulic equipment against work produced at the output end during operation (hydraulic power). It is expressed in percentage form i.e., (output / input) * 100%.
- Noise & Vibration Check-up: While observing other things about it, listen carefully for any strange sounds emanating from your machine, which might be indicative of mechanical troubles or imbalances.
- Results Recording: Always record all readings taken during each particular session plus relevant conditions prevailing then. These records should be kept safely over time because they greatly help one notice trends that may require specific attention later on and assist in making proper maintenance decisions.
Through these few simple guidelines, we will be able to evaluate our hydraulic pumps effectively, detect potential problems early enough, and save them from further damage, thereby prolonging their life span.
What Equipment Is Needed to Test a Hydraulic Pump?
To test a hydraulic pump effectively, you will need the following:
1. Pressure Gauge
- It measures discharge pressure and ensures it conforms to the manufacturer’s settings.
2. Flow Meter
- This is used to check the pump’s rate of output flow. It gives critical information about how well the pump performs under different loads.
3. Digital Multimeter
- If electrically driven, evaluate whether electrical parameters such as voltage and current to be supplied are correct or not.
4. Vibration Analyzer
- It measures vibrations that can indicate mechanical issues or imbalances, thereby showing any signs of wear or misalignment.
5. Thermometer
- It monitors operational temperatures so that pumps do not overheat but work within specific temperature ranges.
6. Calibrated Measuring Cylinder
- Used for manual measurement of volumes pumped during flow tests; hence they should be accurate.
7. Torque Wrench
- It serves to tighten fasteners according to their specifications, which is important in maintaining system integrity.
8. Leak Detection Dye
- This dye helps identify and confirm leaks within systems.
9. Safety Equipment
- Personal Protective Equipment (PPE) like gloves, goggles, ear protection etc., should be worn by operators during testing for safety reasons.
10. Documentation Tools
- Notebooks or digital devices may be needed for recording results obtained from tests carried out on hydraulic pumps, together with observations made so far regarding their performance levels vis-a-vis maintenance requirements, if any.
These tools provide an all-encompassing evaluation of whether or not safety standards were met while operating this type of machinery. Therefore, proper calibration and use based on technical specifications must never be overlooked when making accurate assessments and troubleshooting them effectively.
How to Prepare the Hydraulic Pump for Testing
There are several steps to take when preparing a hydraulic pump for testing. These measures must be followed to make accurate measurements and protect the safety of the personnel involved. This guide is based on recommendations from trusted sources:
1. Initial check-up
- Check for leakages: Make sure no visible signs indicate leakage around the pump or its connections. All seals should remain intact.
- Confirm connections: Ensure all electrical and hydraulic lines have been well fastened and are free from damage.
2. Fluid level assessment
- Hydraulic fluid: Fill up the hydraulic reservoir with the appropriate type (ISO 46 or ISO 32 usually) as recommended by the manufacturer’s instructions.
- Contamination check: Examine cleanliness levels by inspecting for contaminants within the hydraulic fluids; this is crucial for efficiency during operation.
3. Review operational parameters
- Pressure ratings: Supply pressure must match the pump’s rated specification, which can range between 1500 and 3000 psi, depending on the application.
- Flow rate: This refers to the amount required per period; due to varying demands within the systems used, typical values lie between 5 GPM and 120 GPM.
4. Verification of electric system
- Voltage supply: Ensure that it falls within allowed limits according to model e.g.,; most pumps operate at either 230V,115V or 480V AC input power
- Control system: Check whether controls and monitoring systems function correctly. These should also be set right.
5. Safety precautions
- Usage PPEs : operators should always wear necessary personal protective equipment when handling hazardous substances such as petroleum products like oils, etc., during tests conducted under abnormal conditions.
- Emergency procedures: Shut-off methods need to be studied and recorded before testing starts so that responders can know what action to take if things go wrong immediately after starting up and equipment being tested fails to put back off mode by shutting switches down manually without thinking twice about it otherwise accidents may happen due carelessness shown towards safety issues surrounding working environment where these machines are operated within.
6. Preparation of documents
- Record keeping: Notebooks or digital devices must be available for jotting down readings taken at different points,observations made, and any abnormality detected during each particular test conducted over time.
These steps will help ensure that your hydraulic system operates reliably and safely throughout testing. Always consult the manufacturer’s manual for detailed instructions on preparing and testing specific pump models.
What Are the Safety Precautions When Testing a Hydraulic Pump?
To secure the operators and machines involved, it is necessary to follow specific safety measures when testing a hydraulic pump. The following are some of the most critical safety concerns based on industry standards:
1. Personal Protective Equipment (PPE):
- Always wear correct personal protective equipment, such as gloves, goggles, and safety boots, to protect against high-pressure fluid leaks and other hazards.
2. Comprehensive Risk Assessment:
- Carry out an all-inclusive risk assessment before starting tests to identify potential dangers and implement required controls.
3. System Isolation:
- Ensure that all parts of the hydraulic system have been fully isolated; locked out; and tagged out (LOTO) so that they cannot be accidentally activated while being serviced or tested.
4. Protocols for Pressure Testing:
- Follow the procedures for carrying out pressure tests. Confirm that all gauges and equipment being used are rated for expected pressure levels lest they fail due to overloading (typical test pressures may vary from 1500 – 3000 psi, depending on the pump).
5. Fluid Handling Procedures:
- Handle hydraulic fluid with care because it can cause slips hence being a potential slip hazard; also ensure any spillages are cleaned up immediately to prevent accidents from occurring.
6. Emergency Procedures and Equipment:
- Train every operator about emergency response actions specific to hydraulic systems; keep fire extinguishers and emergency shut-off valves easily accessible at all times plus ensure they are functioning correctly.
7. Ventilation:
- Provide adequate ventilation within the testing area, especially if working with hydraulic fluids that could emit fumes or particles that might be harmful to people nearby.
8. Proper Tool Use and Inspection:
- Use tools designed for use in hydraulics only, then inspect them beforehand to ascertain their suitability for the task at hand and check whether any are faulty or unfit for purpose.
9. Training / Competency:
- Ensure that persons carrying out tests have undergone relevant training on how such processes should be done, including knowledge about different types of controls applicable during various stages of testing. Also, ensure they are well-versed in safety precautions about hydraulic systems.
10. Documentation of Findings:
- Maintain detailed records showing what was done during a test, results obtained, safety checks carried out, and abnormal things noticed throughout testing to keep the history of operations clear while still complying with safety standards.
Following these steps will enable the operators to minimize the risks associated with testing hydraulic pumps and at the same time ensure their safety plus efficiency.
How to Use a Flow Meter to Test a Hydraulic Pump
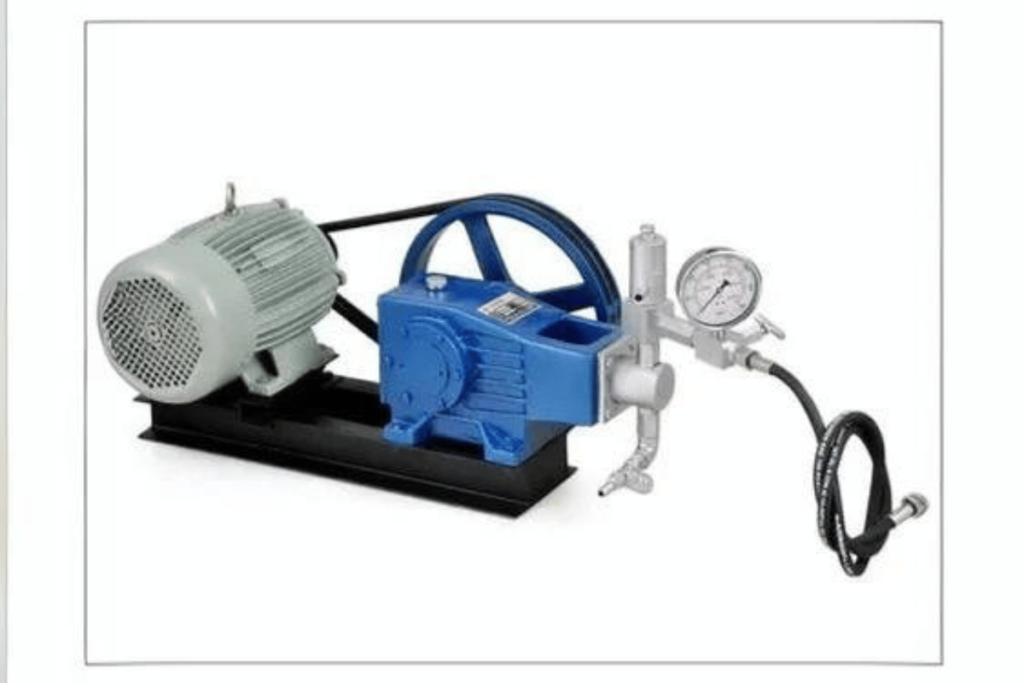
To test a hydraulic pump using a flow meter, use these brief instructions:
- Choose the Right Flow Meter: Select a flow meter corresponding to the flow range and type of fluid used in your hydraulic system. Some common types are turbine, electromagnetic and positive displacement.
- Prepare the System: Ensure that the hydraulic system is shut down and depressurized before connecting the flow meter. This step is important for safety and accuracy.
- Connect The Flow Meter: Mount the flow meter on the hydraulic pump’s discharge line. Make sure it is oriented correctly according to the manufacturer’s instructions (usually indicated by an arrow on the meter).
- Calibrate The Flow Meter: If necessary, calibrate the flow meter following the manufacturer’s guidelines to provide accurate readings.
- Restart The System: Power up the hydraulic system and let it come up to operational status. Check for leaks around connections of flow meters while monitoring them continuously.
- Take Measurements: Observe the flow rate displayed on the flow meter while the system is running. Record values at different operating conditions to see how the pump performs under various loads.
- Evaluate Results: Compare readings of flow rate against specifications provided by pump supplier or manufacturer, indicating whether or not it is working well and whether attention may be needed if there are any deviations from this standard.
- Record Findings: Keep detailed records about measurements taken during testing, such as the date,time,flow rate measured, etc.This will help you in the future when planning maintenance activities based on these findings.
By following this guide, one can effectively use a flowmeter to evaluate the performance of hydraulic pumps, ensuring their efficiency and reliability.
How Does a Flow Meter Work for Hydraulic Testing?
Flow meters measure the rate at which liquids or gases flow through a system. During hydraulic testing, these meters work on different principles, such as mechanical, thermal, or electromagnetic.
- Mechanical Flow Meters: Positive displacement meters belong to this category because they monitor the movement of their components, such as rotors and gears, which rotate in response to fluid motion. They measure volume accurately after calibration through speed.
- Electromagnetic Flow Meters: These devices operate based on Faraday’s law of electromagnetic induction; according to this principle, when conductive fluids move past a magnetic field, it produces a voltage proportional to velocity, which we can use to compute flow rates.
- Thermal Mass Flow Meters: The heat lost by flowing liquids passing temperature sensors is what determines the rate at which these meters measure mass. This provides quantifiable outcomes necessary in hydraulic tests.
Technical Parameters
- Flow Range: Flowmeters can usually have very different operational ranges, with some measuring from a few liters per hour up to several thousand liters per minute.
- Accuracy: Depending on type and calibration ±0.1% – ±5% accuracy relative to actual quantity being measured may be achieved by different models of these devices.
- Response Time: Flow meter readings should take less than one second because systems are dynamic, and they must change quickly enough not to delay.
- Pipe Size Compatibility: There are certain sizes that should match each other if one wants them all working together effectively otherwise there won’t any success in making anything work well so compatibility matters here too much especially when dealing with small bore pipes under 1 inch or large industrial systems over 12 inches diameter size range which could fail without appropriate choice made during selection process depending on need at hand like space available among others.
- Fluid Characteristics: Liquids’ conductivity and viscosity have significant influence over reliability. Electromagnetic ones demand conductive media, while viscosity affects other types, all of which are necessary for reliable measurements, especially during hydraulic tests.
It is important to consider these characteristics and principles so as to use flow meters well in hydraulic testing, which would help in accurately evaluating system performance based on this understanding.
How to Measure the Flow Rate with a Flow Meter
To measure the flow rate using a flow meter, one must follow specific steps in a particular order for accuracy and efficiency. Below is a quick guide built on various authoritative sources’ recommendations:
- Choose the Right Flow Meter: The type of fluid, flow features, and application needs should guide you in selecting a flow meter. Accuracy, range, and pipe size compatibility are some parameters to consider.
- Installation: Correct installation is critical. Place the flow meter in a straight section of the pipe (with enough space before and after it), away from bends, valves or fittings that may cause turbulence and affect its accuracy.
- Calibration: You must calibrate your device according to the manufacturer’s instructions before using it; otherwise, readings will be unreliable and inconsistent.
- Connect Power Supply: Establish a connection between the power supply source(s) required by your specific flowmeter model, ensuring tightness so that there won’t be any interruptions during use.
- Initiate Flow: Start flowing the liquid through system. Give room for stabilization – this might take a few seconds, depending on which type of flow meter was employed.
- Read Flow Rate: Look keenly at displayed figures indicating the rate at which fluid is passing on average over the time interval recorded by the instrument (flowmeter). Be conversant with the units used because some meters provide readings in liters per minute (LPM), gallons per hour (GPH), etcetera.
- Monitor & Record Data: Continuously check reading against expected values, especially where there are no changes in design or functioning known to occur over long periods, such as fluctuation points caused by wear-tear problems associated with high-speed rotating machines like pumps.
Noted Technical Parameters
- Flow Range: It is important to validate whether the chosen device can safely cover anticipated levels of fluid velocities during measurement exercise failure, which could result in damage or malfunctions due to wrong sizing for different ranges of flows encountered.
- Accuracy: ±0.1% up to ±5% accuracy range allows one make dependable conclusions from obtained measurements for further analysis leading to informed decisions.
- Response Time: A less than one-second response time enables the system to track changes in flow conditions as they happen, for instance, when dealing with dynamic systems with variable flows.
- Compatibility with Pipe Sizes: Using correct pipe sizes prevents under-sizing or over-sizing an instrument relative to its applications thereby introducing errors during readings taking.
- Viscosity and Conductivity of Fluids: These properties must be considered, especially where certain types of meters are used, because failure may directly affect accuracy levels and selection criteria adopted by electromagnetic flowmeters, which require conductive media.
Following this procedure while considering main technical parameters will facilitate accurate measurement of hydraulic flow rates, thereby enhancing operational efficiency and reliability in various systems.
What Are Common Issues Indicated by a Flow Meter?
Flow meters are capable of showing a variety of common problems in hydraulic systems. Below are some of the most common problems and their corresponding technical parameters:
- Incorrect readings: This can be caused by wrong calibrations or a faulty flow meter itself. To get accurate measurements, it is important to ensure Accuracy within the specified range (±0.1% to ±5%).
- Fluctuating Flow Rates: Rapid change in flow rate may indicate presence of blockages or leaks along the pipeline. This requires a quick response time, which should not exceed 1 second.
- Cavitation: Cavitation occurs when the flow pressure falls below liquid vapor pressure, leading to the formation of vapor bubbles, which can greatly distort flow measurement readings. It often shows up as jitters and, therefore, underscores the importance of ensuring that the Flow Range matches other components’ specifications.
- Pressure Drops: A significant decrease in pressure could mean there is an obstruction or equipment failure somewhere downstream from this point. Regular monitoring should be done on Pipe Size Compatibility to ensure the meter operates within the designed limits for a given pipe diameter.
- Viscosity Problems: Alterations in fluid viscosity cause incorrect measurements; this mainly affects those types sensitive to Fluid Characteristics, such as electromagnetic flow meters, which require conductive fluids for operation.
- Temperature Fluctuations: Changes in density and viscosity brought about by fluctuating operating temperatures affect accuracy in measuring flows.
- Contamination: Foreign particles like dirt may clog up parts, rendering them useless or providing wrong readings altogether; it is, therefore, necessary that Fluid Characteristics are checked against operational requirements for any given metering instrument on a regular basis.
- Mechanical Failure: Components wear out over time thus reducing performance levels; Reliability monitoring involves routine inspection during maintenance works carried out alongside Technical Parameters assessment relating each specific device being used at site.
- Calibration Error: Consistent inaccuracies due to improper calibration need frequent recalibration to maintain and ensure reliable flow measurements.
- Power Supply Problem: Electronic flow meters require uninterrupted power supply, which can cause a power supply failure, disrupting functionality, leading to inaccurate data collection and extended response time.
These are just some examples among many others refering to common problems found in hydraulic systems, if people know them together with their related technical parameters then they will be able to optimize performance as well as reliability where necessary during flow measurement system installations.
What Is the Difference Between Testing Variable and Fixed Displacement Pumps?
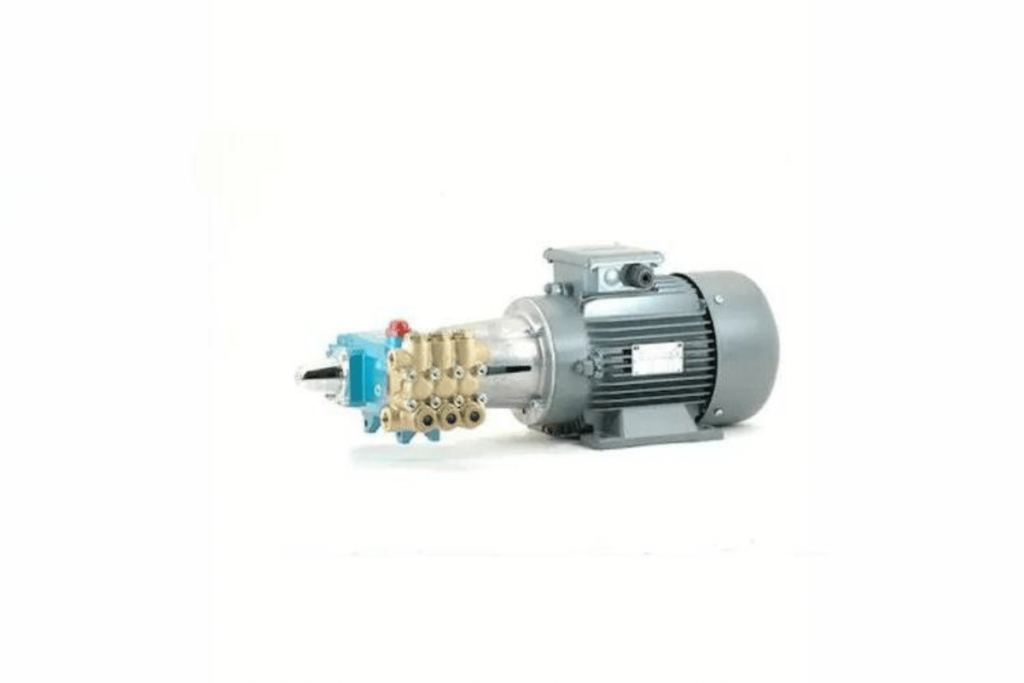
To check pumps’ efficiency, one needs to understand whether the flow rate can be adjusted. The way they work and how flow rates are measured during operation are the main differences between fixed displacement and variable displacement pumps. Fixed displacement pumps have a certain capacity per turn, which means that their flow rates can easily be anticipated and determined when there is no motion. In this case, the evaluation should mainly cover pressure against design requirements about energy losses through leakage being ignored.
On the other hand, it is essential for us to also to note that variable displacement pumps do respond differently depending on what load changes were made into such machines. It implies, therefore, that during testing these varieties of equipment, different operational situations must be taken into account while monitoring them simultaneously with changing loads and control system alterations. Such diversity calls for more dynamic methods of testing which will enable recording various flows at different moments as required by varying demands imposed by systems served by these gadgets.Reality must be watched vividly since complex tests involving live performance indicators are necessary for optimal functionality and responsiveness while dealing with variable displacement pumps at all times.
How to Test a Variable Displacement Pump
Many necessary steps have to be taken, and specific technical parameters need to be considered when testing a variable displacement pump to guarantee accurate performance evaluation. Here is a brief guide developed from various authoritative sources:
1. Preparation: Make sure that the installation of the pump is correct and all connections are tight before starting the test; use the right fluid and fill up the system so as to avoid cavitation.
2. Setting Up The Test Bench: Provide a flow meter, pressure gauge, and other necessary control devices for on a test bench. Create an environment where it is possible to keep track of such factors as input/output pressures, flow rates etc.
3. Establish Baselines: Measure how well the pump works when there is no load on it, i.e., record readings for minimum and maximum flow rates, among other inherent characteristics.
4. Dynamic Testing: Varying flow rate should be observed each time different displacements are made by adjusting controls through which the displacement of pumps can be changed manually or automatically. Some key things you may need monitor are;
- Flow Rate: Verify whether or not this meets specifications at different displacements
- Pressure Differential: Track pressure oscillations to determine efficiency gains/losses; try not to allow them to fall beyond the manufacturer’s recommended values, usually between 5 psi and 10 psi.
- Temperature Probe Positioning / Selection: Select appropriate location(s) for temperature sensor(s) during tests – near overheating-prone areas, mainly around casing where hot spots may occur but still within the range specified, e.g., (180–200°F).
5. Load Testing: Change loads applied against the pump’s capacity while checking response times required for stabilization. Observe how long it takes after adjustment until steady state conditions are achieved based on either pressure or flow rate indication.
6. Leakage Test: Examine if any liquid leaks exist near seals/joints by looking out for signs like dampness/wetness around those places . Consider external limited leaks given under technical specifications i.e., maximum allowable external leakage rates.
7. Documentation: Record every single reading taken meticulously. If there are deviations from what has been recorded against the manufacturer’s charts, it could mean that something is wrong somewhere during operation or even the performance stage.
8. Evaluation: Compare test results obtained with design values set up earlier. Ensure that all observed parameters fall within specified limits for each parameter tested; otherwise, further investigate why such differences occurred and take corrective actions where necessary.
Adhering to these instructions and closely observing given guidelines should allow one to conduct accurate tests on variable displacement pumps under different operational conditions so that they perform optimally.
Steps to Test a Fixed Displacement Pump
To effectively evaluate the efficiency of a fixed displacement pump, one needs to test it systematically. Here are some of the things that you should do:
1. Initial Inspection: The pump should be visually inspected for any signs of damage or wear. It is also essential to check whether all connections, fittings and mounts are tight.
2. Testing Environment Setup: Ensure that safety measures have been implemented within the testing area. Fix the pump on a test rig that can accurately measure flow rate, pressure, and temperature.
3. Flow Rate Measurement:
- Technical Parameter: Flow meters that are already calibrated should be used in measuring flow rates at different intervals.
- Justification: This will help confirm whether the pump can achieve its maximum output, as indicated by its rating.
4. Pressure Testing:
- Technical Parameter: Run the pump while recording discharge pressures.
- Justification: Pressure monitoring enables one to know whether or not such equipment operates within its design limits, i.e., consistently producing steady outputs at expected levels of pressure.
5. Power Consumption Check:
- Technical Parameter: Measure power draw in kilowatts or horsepower units.
- Justification: Power utilization analysis gives insights into this machine’s energy efficiency and identifies potential problems associated with running costs.
6. Temperature Analysis:
- Technical Parameter: Take readings for both fluid temperatures and those of outer casings covering pumps themselves.
- Justification: Increased heat could be an indication either of blockages caused by friction or other factors that might affect performance adversely, thereby reducing their lifespan considerably too soon;
7. Vibration Monitoring:
- Technical Parameter: Determine vibration amounts using meters explicitly designed for this purpose alone
- Justification: Vibration detection plays a vital role in highlighting precise places where misalignment problems may exist alongside component wear, leading ultimately even catastrophic failures occurring sooner than later;
8. Documentation – Make sure you record everything accurately, including operational parameters used during tests along with any strange observations made while conducting them so far;
9. Comparison against Specifications – At the end compare recorded values against the maker’s data sheet so verify whether they met all expectations or not;
10. Final Evaluation—Review the outcome results, after which decide what adjustments, if any, need to be made based on the findings eventually arrived at.
These guidelines are key in ensuring that you have tested a fixed displacement pump for its maximum performance.
Common Issues in Variable Displacement Pumps
Variable displacement pumps, though versatile, face many common problems that can affect their efficiency and performance:
1. Cavitation
- Technical Parameter: Check the inlet pressure.
- Justification: Low pressure at the inlet can lead to cavitation, which causes severe damage to the pump’s internal parts and reduces its effectiveness.
2. Control System Malfunctions
- Technical Parameter: Verify electronic control signals and feedback loops.
- Justification: Control system failures may prevent the pump from adjusting its displacement as required leading to inconsistent output pressures.
3. Increased Wear and Tear
- Technical Parameter: Measure operational hours and fluid conditions.
- Justification: Extended periods of operation without maintenance can accelerate wear on inner components thereby degrading performance.
4. Seal Leaks
- Technical Parameter: Look for fluid leakage around the seal area.
- Justification: When seals become worn out or damaged, they allow fluids to escape, leading to system pressure loss and reduced overall efficiency of the device.
5. Overheating
- Technical Parameter: Observe fluid and casing temperatures.
- Justification: Too much heat could indicate a lack of lubrication or other external factors affecting performance, which may result in the pumping machine’s failure.
6. Improper Adjustments
- Technical Parameter: Review displacement settings against recommended values.
- Justification: Wrong modifications made on displacement mechanism will cause flow rates or pressures that do not meet operational requirements thus rendering them ineffective for use..
7. Contaminated Fluids
- Technical Parameter: Examine fluid for particulate matter content as well as viscosity levels .
- Justification: The presence of contaminants leads to blockages within channels, hence increasing wear tear, greatly impairing reliability and significantly reducing the performance capabilities exhibited by pumps over time.
8. Misalignment
- Technical Parameter: Correctly align the shaft with the coupling during the installation process.
- Justification: Failure to align these two components properly results in vibrations whose intensity increases progressively due to misalignments, ultimately leading to failure, necessitating correct installation procedures followed strictly, especially during maintenance works undertaken periodically if necessary, so that such incidents are minimized, if not entirely eliminated.
9. Suction Line Restrictions
- Technical Parameter: Measure flow rates and pressure drops in the suction line.
- Justification: Blockages along this pathway will decrease efficiency and increase the possibility of frequent cavitation events around pumping systems.
10. Hydraulic Fluid Quality
- Technical Parameter: Regularly test fluid’s cleanliness level and ensure that there is always enough supply within the system.
- Justification: Poor-quality hydraulic fluids do not provide sufficient lubrication, increasing the wear-tear rate among various parts and eventually leading to component failures, which could have been avoided had better grades been used right from the start.
Operators can effectively maintain the operational integrity of variable displacement pumps by being aware of these common issues and closely monitoring the related technical parameters. It is necessary through routine tests following specifications for desired performance levels to be achieved continuously over long durations.
How to Interpret Test Results?
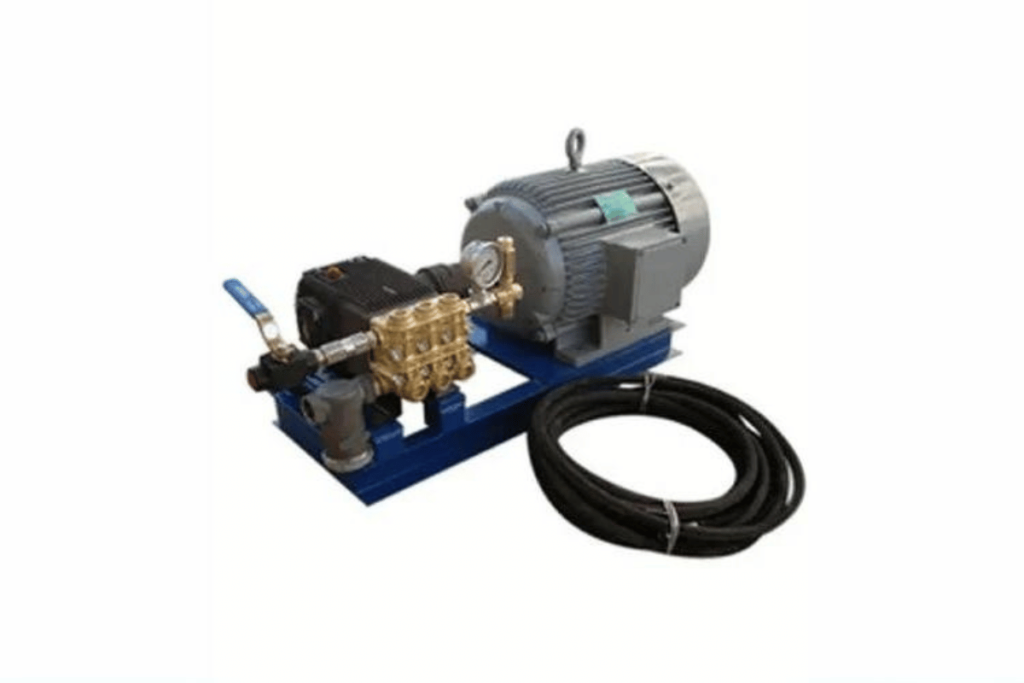
A closer look at interpreting test results for hydraulic pumps shows that it means critically examining the information collected through tests in light of certain standards. Among the indicators of performance are flow rates, pressure differentials, and system efficiency. In evaluating these findings, you should start by comparing measured values against the manufacturer’s specifications.
In the case of fixed displacement pumps, one should check how uniform their flows are and whether there is any leakage detected while dealing with variable ones; on the other hand, this involves considering a pump’s reaction to load variations and its capability of maintaining desired pressure levels. Furthermore, also take note of successive tests trends which could be indicative or wear out signs such as imminent breakdowns and ensure investigation done on unexpected changes too. Flow versus pressure curves, among other graphical representations, can serve to clarify the understanding of pump performance.
Understanding Pressure and Flow Readings
To operate hydraulic pumps effectively, it is necessary to understand pressure and flow measurements. Pressure readings show how much force the liquid within the system exerts, while flow readings determine the volume of fluid that moves in a given time. When such signs are interpreted correctly, operators can detect anomalies, maintain performance levels, and prolong the life spans of pumping machines.
Some of the critical technical parameters functional in the analysis of pressure and flow indicators are:
- Pressure Differential: This measures the difference between inlet and outlet pressures, which reflects pump efficiency or possible blockages, such as wear on pumps or clogged systems themselves.
- Flow Rate: Usually measured in gallons per minute (GPM) or liters per minute (LPM), this parameter helps determine if a given pump is working at its designed capacity level. Deviations from expected values may indicate cavitation problems or faulty pump operation.
- System Efficiency: It is defined as the ratio between useful output power of hydraulic system over input power into it. Lower efficiency readings could mean energy has been lost due to leakages or wrong choice/sizing of pumps.
- Temperature Readings: High temperatures degrade fluids and components used in hydraulic systems, but more so those found within pumps themselves. Therefore, monitoring temperature becomes very important for safe working conditions and predictive maintenance purposes.
These aspects should be looked at alongside other relevant information collected so far by an operator during the measurement process; this way, they will be able to identify potential problems early enough before they become costly failures while also improving reliability and availability rates for these types of machines.
How to Analyze the Temperature of the Pump Case
For the duration of the hydraulic pump’s life and its trouble-free running, it is necessary to check how hot is the pump case. Several steps should be taken:
- Use temperature measuring instruments: You can mount thermocouples or infrared sensors on a pump case to measure its temperature continuously. This enables you to collect data in real time and recognize abnormal temperature variations.
- Define basic temperatures: Depending on what kind of pumps do you have and where are they applied, determine normal working ranges for temperatures hereof. Such standard indicators help find out deviations pointing at underlying problems.
- Control operating conditions: When monitoring these objects, consider factors such as ambient temperature, fluid type, pressure change, etc., because all these things greatly influence them. For instance, high air temperatures or viscous fluids may cause extra heat generation during operation.
- Look through temperature rise tendencies: Make sure that you watch temperature trends from time to time. If they arise slowly, components might wear off, or lubrication is not sufficient; if there are sudden jumps, some parts might fail or clog up.
- Compare with pressure and flow readings: Analyze temperature readings together with those showing pressure differential across certain areas within system (between points) as well as flow rate along pipelines (between sections). When it is noticed that the has risen considerably but flow sharply then, cavitation occurs; otherwise, impeller failure threatens soon.
- Carry out maintenance measures: Based on the results obtained using this method, decide upon necessary repairs or changes in operational mode designed to prevent overheating. This may include leakage detection, checking liquid level adequacy, ensuring normal workability of cooling systems, etc.
The closer operators follow these indicators and implement good diagnostics, the better hydraulic pumps will perform over time without any unexpected downtimes.
What Do the Results Tell About Hydraulic Pump Condition?
The results acquired from checking hydraulic pump parameters will disclose a lot about the condition and performance of the pump. Some of the technical factors that should be looked at are as follows:
- Temperature: As mentioned earlier, unusual temperature readings can indicate some problems. High temperatures are usually caused by too much friction, poor lubrication, or system overloading, which leads to wear and tear and, thus, pump failure.
- Pressure Differential: This measures how efficiently a pump is functioning. If there is a decrease in pressure differential, it could mean that impellers have worn out or the suction line has blocked. On the other hand, a sudden rise may imply system restrictions requiring further investigation.
- Flow Rate: This reading helps us know what amount this particular machine can handle at once. When flow rates drop significantly, there might be cavitation occurring within it. Also, the machine wears off quickly due to unhealthy system joints, leading to leakage problems.Consistency in flow rates should always be maintained for better performance.
- Vibration Analysis: An increase in vibration levels can occur when there is misalignment between different parts of machines, cavitations, or even internal wear during their operation cycle phases. Therefore, it’s advisable that one carries out frequent checks, especially if these components are affected, because they should be replaced on time before causing any serious damage elsewhere.
- Lubrication Levels: Properly lubricating all moving surfaces reduces frictional forces between them, thereby reducing the rate at which they wear out, hence extending their life span too. Failure to do so will result into elevated temperatures brought about by continuous rubbing against each other thus accelerating component degradation beyond repair.Low levels of lubricant could lead to such events happening within our systems; therefore, we must ensure oil content remains optimal throughout the entire process.
Through analyzing these parameters, operators can get detailed information concerning the healthiness of hydraulic pumps, addressing potential problems early enough and enhancing overall operational efficiency.Regular assessments based on these indicators, together with following maintenance schedules, are vital for prolonging the lifespan of pumps as well as ensuring they serve reliably.
Frequently Asked Questions (FAQs)
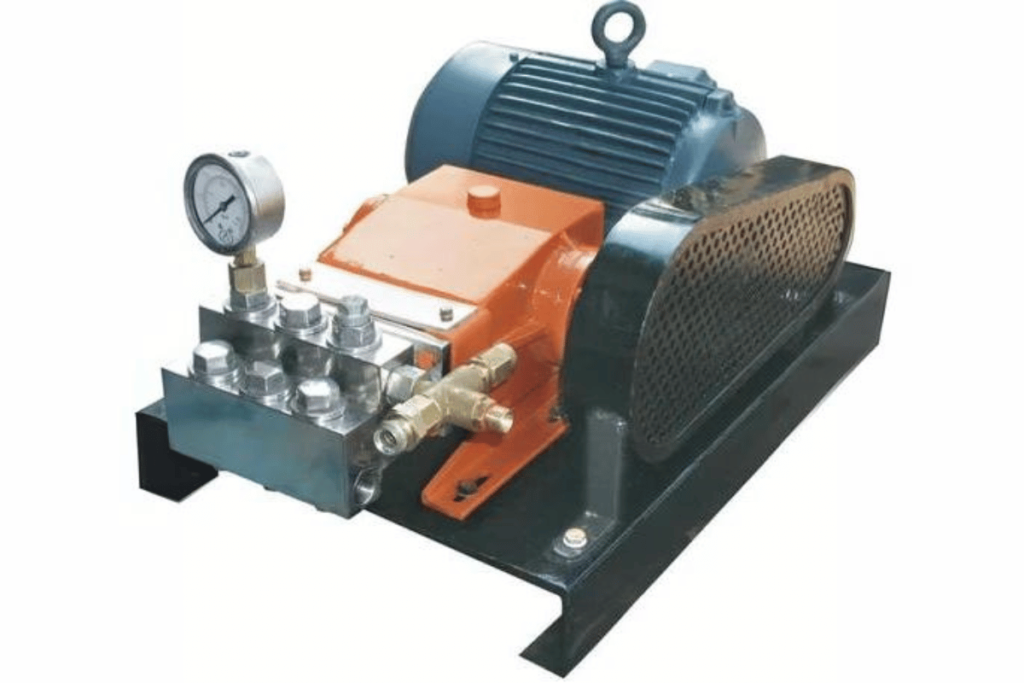
What causes hydraulic pump failure?
Hydraulic pump failure can be attributed to several factors, including excessive temperatures, pressure differentials, low lubrication levels, and mechanical wear. Regular monitoring of these parameters helps in early detection of potential issues.
How can I determine the efficiency of my hydraulic pump?
To assess the efficiency of your hydraulic pump, regularly measure the pressure differential. A significant change in this metric can indicate either wear or blockages, which require immediate attention.
Why is flow rate important in hydraulic systems?
Flow rate is critical as it reflects the pump’s operational capacity. Significant drops in flow rate could signify problems like cavitation or leaks, adversely affecting system performance.
What role does vibration analysis play in pump maintenance?
Vibration analysis helps identify mechanical issues such as misalignment or internal wear. Monitoring vibration levels regularly allows for timely maintenance, preventing more severe failures.
How often should I check lubrication levels?
Lubrication levels should be checked regularly, as proper lubrication is essential to reducing friction and preventing overheating. Establishing a routine maintenance schedule can help maintain optimal levels.