Kawasaki is one of the leading brands in hydraulic pump industry that manufactures high-quality hydraulic pumps for a wide range of industrial machinery. Their pumps are renowned for their dependability, strength plus incomparable performance. In this article, we will discuss Kawasaki hydraulic pumps’ characteristics and merits as well as tips on how to control and troubleshoot these advanced machines.Hydraulic pumps are vital elements of industrial machinery since they provide the power needed for operation of hydraulic systems. Kawasaki hydraulics work by transforming mechanical energy into hydropower which is then used to run various pieces of equipment in industrial machinery. Proper manipulation of hydraulic pumps is important to maintain peak performance while preventing machine damage.
The significance of controlling a hydraulic pump in an industrial machine cannot be emphasized enough because it directly influences its efficiency, productivity and durability. If properly controlled using the right techniques and maintained regularly, industrial machines may perform optimally giving reliable and consistent service. The following sections will cover different types of Kawasaki hydraulic pumps, advanced control techniques, troubleshooting tips, advantages and future development plans.
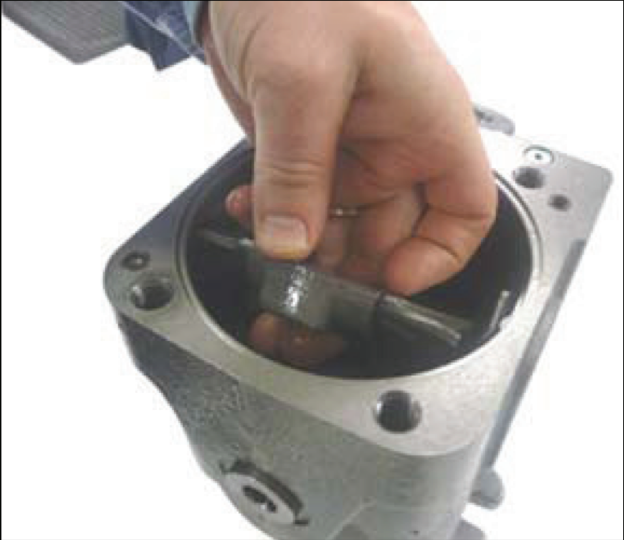
Various Types of Kawasaki Hydraulic Pumps
There are various types of hydraulic pumps that Kawasaki provides to suit different industrial applications as follows:
Axial Piston Pumps Axial piston pumps are one of the most widely used hydraulic pump categories by Kawasaki. They have a swash plate to control the angle of the pistons so as to adjust fluid flow depending on system requirements. The K3V/K5V series of axial piston pumps provide high durability and performance for Kawasaki.
External Gear Pumps These consist of two gears, an inlet gear and an outlet gear, which rotate causing a vacuum that pulls in fluid while the pressure created by gears pushes it out. This external gear pump series is recognized for its high efficiency and quiet operation by Kawasaki.
Internal Gear Pumps Kawasaki’s internal gear pumps are suitable for medium to high pressure applications because they include an inner rotor with external teeth and an outer rotor with internal teeth. When the inner rotor rotates, it results into rotation of the outer rotor thus creating a vacuum which draws in fluid. Excellent performance and reliability is what can be expected when using K3VG series internal gear pumps from Kawasaki.
Radial Piston Pumps In this type of pump, there is a central shaft with radially arranged cylinders having pistons inside them. The rotation of shaft moves these pistons thereby causing a vacuum that sucks in fluid. With the capability for high flow rates at relatively higher pressures, radial piston pumps under K8V series from Kawasaki are known to deliver such features.
Bent Axis Pumps Bent axis design which enables mechanical energy transformation into hydraulic energy is employed in bent axis pumps from Kawasaki. By adjusting this angle, it controls liquid flow rate through device for efficient functioning purposes. Designed with compactness and higher efficiency in mind; these qualities define K3X line series amongst bent axis pumps manufactured by Kawasaki.
Each type has unique characteristics and advantages among various types of hydraulic equipment made by Kawasaki, and thus can be used in different applications. Therefore, it is necessary to carefully consider the demands of the system and choose a pump that will optimize performance.
Advanced techniques in controlling Kawasaki hydraulic pumps have been advanced besides the fundamental control techniques. Basically, these advanced techniques allow for more accuracy or precise control of the pump. They are also aimed at improving the entire performance of industrial machines. There are two of the major advanced control methods which include electronic control and variable displacement.
In electronic control, hydraulic pumps are controlled using electrical sensors and controllers. This allows for more accurate control as the system reacts real time to change in operating conditions. With electronic control, a pump will be able to raise its output while matching that required by the system thus leading to efficiency and productivity improvement.
Variable displacement is another kind of sophisticated control technique that permits a hydraulic pump to regulate its output based on system load demand. Hence, it means that the pump adjusts its output in line with demands from within it thereby raising efficiency while reducing power consumption levels as well. Industrial machines experiencing varying loads throughout operation find this method important.
Additionally, proportional control and closed-loop control systems can also classify as some other sophisticated techniques used for controlling hydraulic pumps. In proportionate controls, there is a direct relationship between input signal and changes in flow rate through the pump; while closed loop controls use sensors to monitor system operations so as to maintain desirable outputs through adjustments on pumps’ volumes.
Essentially, advanced Kawasaki hydraulic pumps’ handling skills result into better performance and efficacy of industrial machines. Incorporating such improvements into hydraulic command structure makes operators get more precision and influence over a pump consequently enhancing cost effectiveness and profitability via increased production rates.
How would you troubleshoot problems with a Kawasaki Hydraulic Pump?
When it comes to hydraulic pumps, Kawasaki hydraulic pumps build up problems as well as malfunctions. As such, quick identification and resolution of these issues is important to avoid costly downtimes and repairs. The following are some common issues that can occur with Kawasaki hydraulic pumps and methods of resolving them through troubleshooting:
Low hydraulic fluid levels: Low level of hydraulic fluid ends in cavitation that can destroy the pump and other parts of the system. It may also cause overheating and collapse of the pump. To troubleshoot this problem, check the level of fluid and add more if necessary.
Pump noise: Strange sounds like knocking, whining or grinding heard from the pump could indicate mechanical problems. If it is the pump producing this noise it could mean bearings or gears that need replacement due to excessive wear. In order to troubleshoot this issue, inspect for worn out components on the pump and replace them where necessary.
Leaks: Leaks can lead to loss of pressure in hydraulic systems resulting into less efficiency for a pump. Look out for any leaks in either seals fittings or lines used for hydraulics and change any affected by physical damage or wear.
Pump overheating: This situation may come about due to low levels of fluids; destructions at various parts; obstruction at cooling systems among others. Investigate fluid levels, assess for damage on parts related to gear box and confirm proper functioning cooling systems during fault narrowing down.
Vibration: Vibration leads to detrimental effects on both the pump and other hydrologic elements. Find out if there are any misaligned shafts, damaged bearings or faulty gears within it which require new replacements on these parts in case they are broken down.
Doing regular maintenance can help prevent these things from happening initially. It is crucial that routine checks are carried out regularly along with maintaining an effective system operation. Besides that, correct fluid type/filtration as provided by Kawasaki are vital.
A hydraulic pump technician is the person to consult with when such matters arise in need of fast and reliable problem diagnosis.
Pros of Kawasaki Hydraulic Pumps
Kawasaki hydraulic pumps come with several advantages for various industries and applications. These pumps are made to be very efficient, dependable and affordable; they have a large appeal to business organizations intending to boost their machine performance.
Efficiency improvement is one of the several benefits of Kawasaki hydraulic pumps. They are designed in such a way that they deliver precise amounts of fluid which helps in reducing wastage as well as enhancing system performance. As a result, there is an increase in productivity coupled with reduced energy consumption thus saving on costs over time.
Versatility is also another key benefit that comes with using Kawasaki hydraulic pumps. There are different types and sizes of these pumps hence they can be used in various industrial applications. For instance, axial piston pumps are common in construction equipment while bent axis ones are popularly used in industries machinery and machine tools.
Moreover, Kawasaki hydraulic pumps also have high durability and long life span. In fact, these machines have been designed to withstand all sorts of work conditions and can last for very many years if properly taken care of. This removes the need for frequent replacements thereby keeping running costs low.
Besides this, Kawasaki hydraulic pumps provide high precision control that enables better accuracy while moving machinery. Additionally, its noise levels together with vibration levels are very minimal making it ideal for application where excessive noise or vibration may be problematic.
In conclusion, companies can rely on Kawasaki hydraulic pump options when seeking ways of improving the efficiency or functioning mechanism within their set up. The businesses can install these devices into their machinery so as to increase efficiency & productivity and reduce cost as well – improve machine performance overall by making them more reliable.
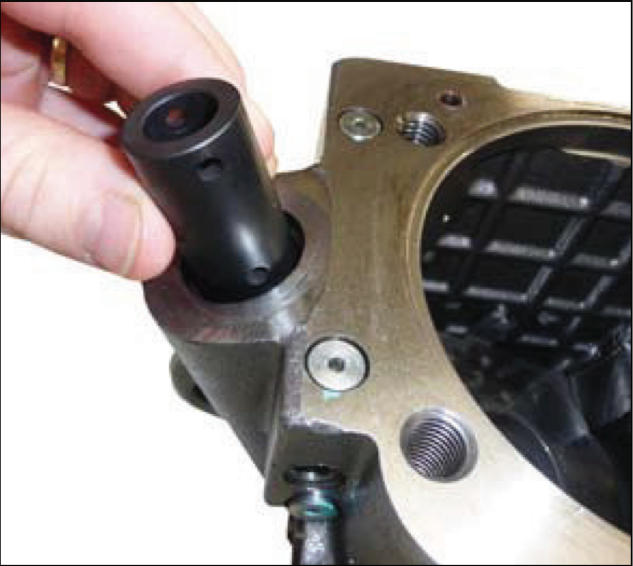
Kawasaki Hydraulic Pumps: Innovations and Future Developments
Kawasaki Precision Machinery’s parent establishment, Kawasaki Heavy Industries, has been a hydraulic pump technology leader for more than 100 years. Over the years and through its commitment to research and development, the company has recorded several milestones in hydraulic pump technology, with a number of exciting ones on the way.
One aspect that Kawasaki gives attention to is energy-efficient hydraulic pumps. Through this means, it introduced a new range of pumps recently that reduce consumption of energy which helps in cutting down running costs as well as reduce carbon emissions. These electronic controlled systems of these pumps are sophisticated enough to optimize pump performance by minimizing energy wastage.
Kawasaki also concentrates on “smart” hydraulic pump technology. This entails utilization of sensors plus other electronics aspects in performing real-time monitoring of the pump performance and making necessary adjustments automatically. These smart pumps are able to increase efficiency and lower system wear by continuously optimizing pump performance based upon changing operating conditions leading to longer life for pumps hence less maintenance cost.
The third strategy employed by Kawasaki is centered on enhancing the dependability and durability of their hydraulic machinery through adoption different manufacturing procedures as well as new materials. These include advanced coatings and surface treatments which prevent wear or corrosion, casting/machining processes allowing for tighter tolerances/ more precisely machined parts.
All these options demonstrate that Kawasaki will remain at the forefront when it comes to development in hydraulic pump technology. The company has positioned itself well in this field due to its strong emphasis on research & development coupled with deep understanding of industrial customers’ requirements will enable it remains delivering groundbreaking solutions that enhance performance as well as efficiencies in hydraulics across various sectors.”
Guidelines for Selecting and Installing Kawasaki Hydraulic Pumps
Choosing the right hydraulic pump to install in a machine is important; this will help it to perform optimally and become efficient. Below are some things that you need to consider when selecting and installing Kawasaki hydraulic pumps:
Application: When purchasing a Kawasaki hydraulic pump, the first thing you would want to look into is its application as well as how it will be used in commercial machinery. For any given industrial process, the pump should have the required flow rate, pressure, and power.
Type of Pump: Kawasaki offers several types of hydraulic pumps such as axial piston pumps, radial piston pumps and bent axis pumps. Each type of pump has its own advantages and disadvantages so it is important to select the right one based on performance requirements and application at hand.
Pump Size: The size of your hydraulic pump also determines how well it will perform. A small sized pump may fail to provide the required flow rate or even pressure while an oversized one can result in wastage of energy thereby reducing efficiency. Choose an appropriate size of a pump depending on your desired flow rate as well as pressure for a particular application.
Installation: Proper installation is critical for ensuring that the hydraulic pump works properly. The manufacturer’s instructions must be strictly adhered to during installation which may include aligning, mounting and connecting hoses/fittings correctly.
Integration: It is necessary for the hydraulic pump to be embedded correctly within the entire hydraulics system of machinery. This entails linking up with reservoirs, valves including actuators as well as guaranteeing proper flow as well as pressure throughout that system.
Maintenance: Regular maintenance helps ensure that your hydraulic pump lasts longer while performing efficiently too. Some routine tasks like replacing filters; keeping check on fluid levels or leakages are very important in maintaining them.
Through considering these factors when choosing and installing Kawasaki hydraulic pumps into their machines, firms can ensure optimal efficiency at all times for the equipment.
Conclusion: Kawasaki Hydraulic Pumps Maximize Industrial Machinery Performance
Industrial machinery is a place where one has seen that Kawasaki hydraulics pumps have been proven to be reliable and efficient. Proper selection, installation, and maintenance of such pumps can make machines perform better resulting in less downtime.
In conclusion, the benefits of Kawasaki hydraulic pumps are many and undeniable. In other words, these pumps are worth their price as they improve efficiency and increase productivity in industrial machinery. The advanced techniques in control of hydraulic pump, problem solving and selecting an appropriate pump for job enabled firms to optimize their machine performance and lengthen equipment life. With improvement in technology, we should expect more innovation from Kawasaki among other hydraulics pump manufacturers leading to enhanced reliability and performance of industrial machines.