In this post, we will discuss why it is challenging to replace hydraulic pumps, which are used widely in the industrial and agriculture sectors. Being aware of the cost of changing a hydraulic pump helps business owners and operators because their maintenance budget and overall efficiency depend on it. Different things such as the type of pumps, labor costs, and frequency with which they need to be serviced affect how much money one should spend on replacing them. So what can readers take away from this article? Well, after reading through all these points about when does one know that their hydraulic pump needs to be replaced or not; then he/she should have no problem making an informed decision that will minimize downtime while ensuring continuous performance in his/her operation area.
What Factors Influence the Cost to Replace a Hydraulic Pump?
There are many things to consider when you look at the cost of replacing a hydraulic pump. These include:
- Type of Pump: The price varies according to gear, vane or piston pumps. Also specialty ones are more expensive because they have specific uses.
- Brand and Quality: What you know about brands and how good they are will affect how long it takes to replace them, too. Pumps with higher quality tend not only to last longer but also balance initial costs against lifetime expenses.
- Labour Costs: The complexity level involved during setup affects labour charges. If workers need special skills or extensive repairs, have to be made around the system, expect high labor costs.
- Other Parts: In some instances changing this machine may call for replacing other parts such as filters seals and hoses which increases the overall amount spent.
- Location: Different areas charge different rates per hour worked, thus accessibility determines transportation fees used alongside repair time spent at an installation site.
- Service Requirements: When these units are not serviced well, additional expenses may be incurred to clean the system or fix other parts.
- Downtime: The quicker one wants a new part installed determines how much money they will pay; normally faster services attract higher charges.
- Warranty & Guarantees: Some firms offer warranties but these can change total costs according to coverage terms and duration periods.
- Market Forces: Material prices can increase or decrease depending on demand fluctuations within industries that supply pumps and related services.
- Consultation Charges: Some enterprises impose fees during initial consultations or assessments thus increasing overall replacement costs slightly above average expectations.
By noting these factors, proprietors can better approximate their possible financial involvement in hydraulic pump replacements, thereby enhancing effective budgeting.
Type of Hydraulic Pump: Gear, Piston, or Vane?
To ensure that you choose the right hydraulic pump, it is necessary to know the three main types: gear pumps, piston pumps, and vane pumps. Each type has unique properties and technical parameters that may suit particular applications better.
1. Gear Pumps:
- Operation: It uses two or more gears to move hydraulic fluid.
- Efficiency: This type usually gives a constant flow and works well at low pressures.
- Technical Parameters:
- Pressure Range: Up to 2500 psi
- Flow Rate: Generally from 0.5 to 10 gpm
- Justification: It is perfect for low-viscosity fluids and applications where there should be an even flow.
2. Piston Pumps:
- Operation: They create hydraulic pressure by using pistons and can change output through displacement.
- Efficiency: At higher pressures, they are better than gear pumps.
- Technical Parameters:
- Pressure Range: Up to 5000 psi
- Flow Rate: Can vary widely, usually from 1 to over 100 gpm
- Justification: They are suitable for high-pressure applications or where variable flow rates are required.
3. Vane Pumps:
- Operation: These work on the principle of sliding vanes creating variable fluid displacement.
- Efficiency: It offers a good balance between pressure and flow.
- Technical Parameters:
- Pressure Range: Usually up to 2500 psi
- Flow Rate: Typically from 2 to 30 gpm
- Justification: They are suitable for moderate applications where compact design and smooth operation are desired.
In summary, what kind of hydraulic pump you choose heavily depends on what you need it for—pressure requirements, flow rate, or the viscosity of the fluid used. Knowing these categories together with their specifications allows one to make informed decisions based on operational needs.
New Pump vs Rebuilt Pump: What’s the Difference?
When considering buying one, it’s essential to understand the differences between new and rebuilt hydraulic pumps.
1. Cost
- New Pumps are typically more expensive because they are brand-new and come with a full manufacturer’s warranty.
- Rebuilt Pumps: Since they’ve been restored, these types of pumps tend to have lower prices which make them good for businesses on tight budgets.
2. Condition
- New Pumps: They are guaranteed to be in perfect condition. In other words, they should meet every specification set by their makers.
- Rebuilt Pumps: As much work as necessary for operation standards is necessary, but there can still be variations in quality depending on how much work was done during reconstruction.
3. Warranty and Support
- New Pumps: In most cases, these come with a long-term warranty that protects against defects caused by manufacturing errors.
- Rebuilt Pumps: Although some might offer limited guarantees which could be very important too.
4. Technical Parameters
New Pumps:
- Pressure Range: Normally follows up-to-date technological standards so it could even touch 5000 psi or beyond that level.
- Flow Rate: It can consistently provide an even higher performance within a wider range over time than any other type, mainly because this category is made for specific applications only, such as those used in the heavy industry sector, where constant pumping power without fluctuations is required during various operational activities like drilling holes through thick concrete walls, etcetera…
Rebuilt Pumps:
- Pressure Range: Based on rebuild quality, it could have slightly altered performance characteristics, although it was still able to achieve initial design requirements regarding pressure levels, etc.
- Flow Rate: Quality issues affecting components used during rebuilding process might lead into fluctuation of flow rate hence this being susceptible aspect as far as rebuilt pumps are concerned…
5. Lead Time:
- New Pumps: Manufacturing may take longer before being ready for delivery due to the production phases involved, such as assembling parts together, testing all functionalities, and packaging them.
- Rebuilt Pumps: Immediate availability often provided thus making it possible to solve emergencies quickly since one can get them anytime without waiting too much longer as would be case when dealing with new ones which must undergo different stages right from manufacturing up until they’re dispatched into market where customers buy according their needs and preferences.
The above means that new pumps are more reliable and use modern technology while rebuilt ones can work just as well if appropriately repaired. These considerations help in making the best choice for specific operational demands.
OEM-Equivalent Parts: Should You Consider Panagon Systems?
In the case of OEM-equivalent parts, especially those from Panagon Systems, some essential elements that must be considered are compatibility, quality and technical parameters. Below are some considerations based on insights from multiple reliable sources which justify going for Panagon Systems:
1. Compatibility:
- Panagon Systems’ OEM-equivalent parts are designed to meet or exceed the specifications of the original equipment manufacturer; hence, they can be seamlessly integrated with existing systems, thereby minimizing the chances of operational disruptions.
2. Quality Assurance:
- According to specific sources, it has been confirmed that there is strict adherence by Panagon Systems to quality control procedures. This means that their components undergo extensive testing to ascertain whether or not they can withstand similar working conditions as those of original manufacturer’s items (OEM).
3. Cost-Effectiveness:
- One may save much money when he/she decides to use OEM-equivalent parts rather than originals without necessarily affecting performance or reliability. In addition, Panagon Systems provides competitive prices coupled with warranties which offer more protection.
4. Technical Parameters:
- Pressure Range: Many a time do parts made by Panagon Systems match or even surpass industry standards concerning pressure where specific applications require such capabilities just like the way OEM specifies.
- Flow Rate: Across various applications, flow rate for OEM equivalent parts manufactured by Panagon Systems ensures operational efficiency is not compromised because it remains constant.
To sum up, considering aspects including but not limited to compatibility, stringent quality assurance measures, and favorable technical specifications can help one make an informed choice about whether or not they should purchase Panagon System’s products, which act as substitutes for the original manufacturer’s items (OEM). It is,, therefore,, necessary to critically evaluate these parameters during the decision-making process in light of operational requirements.
How to Identify When Your Hydraulic Pump Needs Replacement?
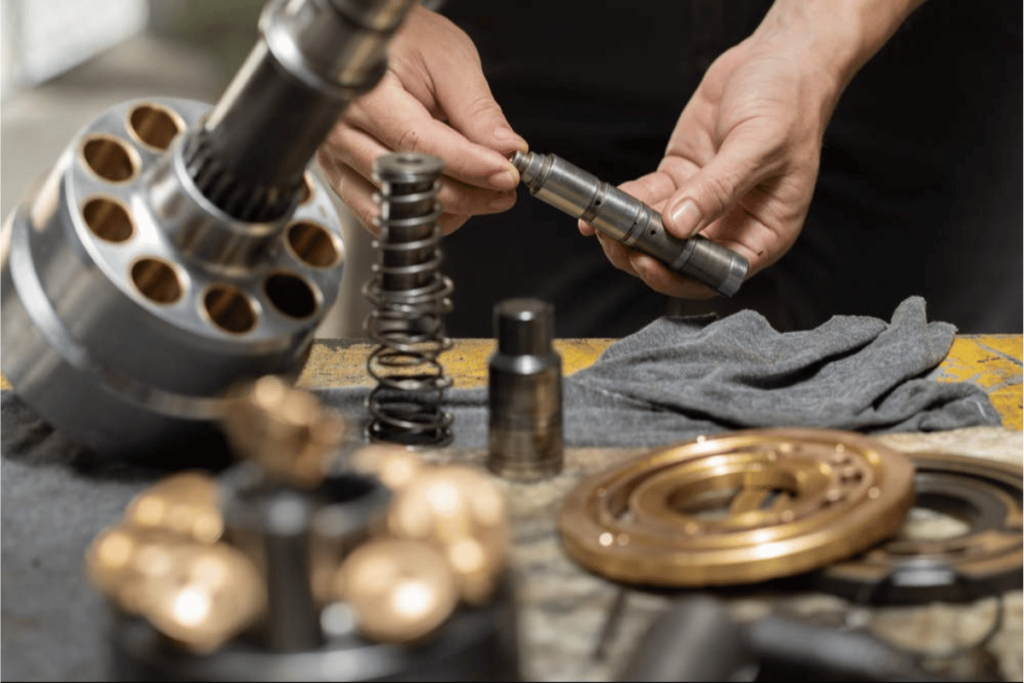
There are several ways to tell if your hydraulic pump needs to be replaced. The first thing you should do is listen for any strange noises such as grinding or whining that could mean it has been damaged internally. Secondly, should there be a significant drop in pressure or performance observed, this would most likely indicate that the pump is going wrong. Leaks around seals on pumps are also an essential sign because they can cause efficiency problems and lead to more significant troubles later on if left unchecked. Another thing you need to keep an eye on is fluid quality; contaminated or discolored hydraulic fluids often show where pumps have been wearing out or getting damaged over time. If a pump frequently gets too hot, it might be because it’s running beyond its capacity or is not sized correctly for the system. Vibrational levels increasing suddenly while pumping could also mean something terrible is happening quickly. Records of maintenance done and the history of operation may speak volumes: if repairs have had to happen often with this one device, or severe wear is obvious, then replacing it is probably best anyway. These things should all be monitored regularly so as not catch oneself off guard when machines break down unexpectedly – thereby keeping them running efficiently!
Signs of Hydraulic Pump Failure
To avoid costly downtime and repairs, knowing the signs of hydraulic pump failure early is important. These are the main warning signs as per various industry sources:
- Strange Sounds: For example grinding noise, whining noise or banging sound that may imply worn out or damaged internal components.
- Pressure Drops: When system pressure drops significantly, it could indicate that the pump has failed. Therefore, it is crucial to keep track of pressure gauge readings for any fluctuation.
- Leaking Fluids: Fluid leaks resulting from bad seals should not be taken lightly because they show potential pump problems.
- Overheating: Should the temperature exceed normal operational limits due to overload or poor cooling, among other causes, this might be considered another form of warning sign that degradation has already occurred.
- Increased Vibrations: If there is too much shaking during operation time, it means alignment errors may have occurred inside or outside, which needs immediate attention before further damages take place, such as cavitation (formation of gas bubbles in a liquid) inside pumps, leading to wear out.
- Contaminated Fluids: Any presence particles or discoloration within hydraulic fluid usually indicates deteriorating conditions around pumps themselves thus one must always ensure cleanliness is maintained throughout so that these devices can last longer without breaking down frequently.
- Erratic Operation: Inconsistency in working patterns, such as speed fluctuation, indicates that something might be wrong somewhere within its circuit .
- Frequent Repairs: When you start experiencing high rates of repair work being carried out on the same item consecutively over short periods, coupled with changing performance figures like flow rate, then expect nothing less than total breakdown as soon as possible.
- Change in System Performance: Poor-functioning equipment powered by such a system becomes slow during operation, which is easily noticeable since sluggishness signifies the presence of some issues related to the pump itself already.
- Age & Maintenance Records: It pays off handsomely if one regularly evaluates service life on basis incremental years towards end-of-life predictions. For this reason any device reaching recommended operational age must have been maintained consistently throughout otherwise there will be no choice but to replace it as soon as possible among other pumps.
Therefore by observing these signs closely and having full records on servicing activities done so far, operators will be in a position to adequately evaluate the condition of their pumps thereby ensuring that they are always running at peak levels within hydraulic systems. Additionally, it is essential to conduct periodic checks against specified technical parameters during regular maintenance routines aimed at promoting longer life span for equipments alongside higher energy efficiency levels too
Common Symptoms: Leaks, Noise, and Performance Issues
- Leakages: Leaks in hydraulic fluid are one of the most common signs that a pump is malfunctioning. They may be caused by, among other things, worn-out seals or loose connections. Deviations – from recommended levels – in terms of pressure and viscosity should be taken into account as some of the technical parameters since they can affect integrity of seals thereby leading to leakages.
- Strange Noise: Unfamiliar sounds like grinding, whining, or knocking could mean mechanical problems are being experienced. Lubrication failure, bearing wear, or gear failure are among the causes of such noises, which usually come from components that have already failed or need lubricating. So operators should monitor decibels during an operation against manufacturer’s specifications.
- Reduced Performance: The flow rate drops, indicating potential pump failure when pressure falls too much. It is important to check this against actual performance data by verifying desired pressure threshold and flow rate parameters versus KPIs (Key Performance Indicators). Inadequate performance often goes hand in hand with internal wear or blockage.
- Heat Build-Up: Overheating while running signifies inefficiency within the pump i.e lack of cooling or being overloaded thermally. What needs to be done here is monitoring temperature readings and ensuring they fall within the manufacturer’s limits lest damage occurs.
By watching out for these symptoms with other technicalities operators can keep their hydraulic system working well and deal with any emerging problems before they become major failures.
Impact of a Failing Hydraulic Pump on Your System’s Performance
A faulty hydraulic pump can largely undermine the general performance of a hydraulic system. This component affects the flow of fluid, pressure and efficiency in the whole setup when it starts failing thereby causing operational problems. Here are some of its impacts:
- Reduced Efficiency—When internal elements become worn out, the pump fails to move liquid effectively, resulting in a reduced rate of flow. Such inefficiency may lead to delays in response time for hydraulic-powered equipment.
- Pressure Drops– Actuators among other system components’ performance may be compromised if adequate pressure levels cannot be maintained due to failure of this device. Operations can slow down or fail entirely under load with low pressure.
- Increased Operating Costs– Energy consumption is usually high where an organization operates a hydraulic system with failed pumps because they are inefficient. In this case, operational costs will go up as systems may require more effort to compensate for deficiencies caused by such pumps.
- System Wear and Tear—Valves, hoses, and seals could fail quickly because they wear out quickly when subjected to harsh conditions brought about by poor functioning of these devices.
- Heat Generation And Efficiency Loss– As earlier mentioned; inefficient pumping causes excessive heat which destroys quality Hydraulic Fluids (HFs). Consequently this situation can also aggravate problems by increasing component wear around seals etc.
Technical parameters to monitor
- Fluid Pressure– The manufacturer sets specific limits for the pressure to stay at all times during operation. Therefore one should check both static and dynamic pressures regularly to ensure uniformity in how the entire system performs.
- Flow Rate– It is important that real time flow rates are constantly measured against what has been provided for in terms of design specifications Failure to do so might indicate presence pump problem areas especially if significant deviations are noticed.
- Viscosity of Hydraulic Fluids—Good practice demands that proper viscosity levels be maintained if efficiency is desired. Extreme values, either high or low, lead to inadequate lubrication and rapid wear out.
- Temperature– Monitoring should be done on the operating temperatures to avoid overheating because such conditions could be catastrophic for any mechanical part. If consistent readings reflect figures above recommended levels then it means some parts within these devices are not working as required hence need replacement or repair immediately.
By observing these parameters operators can easily detect hydraulic pump faults and fix them appropriately thus keeping their systems running smoothly.
What are the different types of hydraulic pumps and what are their costs?
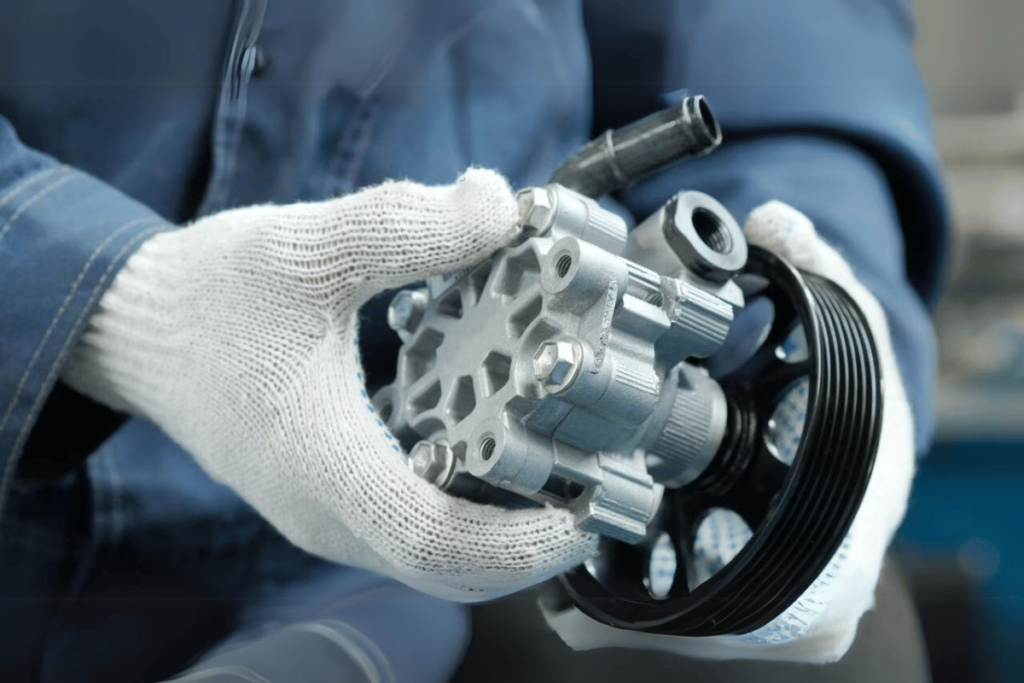
Hydraulic pumps have different types depending on each type’s application and performance requirements for unique operations. The commonly used types are:
- Gear Pumps: These are simple in design and widely used because of their durability and efficiency in terms of performance. Depending on the size and manufacturer, they usually cost between $100 to $2,000.
- Piston Pumps: Piston pumps have high-efficiency levels and varying pressure capacities. They can be bought for around $250, but depending on the specifications, they can cost more than $5,000.
- Vane Pumps: These pumps are efficient and often used in moderate-pressure applications. The typical price range for vane pumps is from $200 to $3,000.
- Screw Pumps: Screw pumps work well with transferring viscous fluids; they’re very effective but also more expensive than other options–they typically fall within the range of about $1,000-$10,000 each pump unit.
- Diaphragm Pumps: Diaphragm pumps are used when precision is required or corrosive fluids need to be handled; they usually cost between approximately 300 dollars and 3500 dollars per pump unit.
The total cost may also depend on other factors such as manufacturers’ names, additional features included with the purchase or specific details about what kind exactly one needs so make sure not only type alone but also overall costs should be evaluated before buying anything. Factors like maker name recognition or added utilities could also increase prices significantly. But most importantly, you should consider your operational need when choosing a hydraulic pumping machine as this will save time & money!
Understanding Gear Pump Costs
When assessing gear pump costs, one must consider many things that can affect the price and general worth. Below are critical factors highlighted by some of the leading industry sites:
- Gear Pump Type: The cost differs between internal and external gear pumps. Typically, an internal gear pump is more expensive due to its ability to handle high-viscosity fluids efficiently; prices range from $300 to $4000, while those of an external gear pump lie between $100 and $1500.
- Rate of Flow: Flow rates for these devices usually given in gallons per minute (GPM) are used as rating units. Indusrial applications require higher flow rates which tend to be priced higher as well. However; standard ones can flow from 1 GPM upto beyond 100 GPM.
- Pressure Ratings: A gear pump’s capacity to withstand maximum pressure influences pricing too because such machines need more robust materials and better construction techniques than their counterparts with lower limits do. Consequently, those rated at higher pressures (1500 psi vis-a-vis 3000 psi) would fetch relatively elevated prices.
- Material Used: The material a pump is made of significantly affects its overall cost, especially if it operates in corrosive environments frequently. Stainless steel models are much pricier than ordinary cast iron or aluminum ones.
- Reputation Of Manufacturer: More often than not established brands have higher levels of dependability built into their products – however, this tends to come at extra charge, which could be justified by more extended warranties offered as well as availability of support services
- Extra Features Included: Additional attributes like adjustable flow settings; built-in pressure relief systems or advanced sealing mechanisms usually attract premium charges attached onto them therefore making them costlier too
Thus, a person should evaluate these variables carefully, considering how well they align with his/her unique application requirements before deciding to select and invest in gear pumps.
Piston Pump Pricing: Is It Worth the Investment?
To assess the cost of piston pumps, there are a few technical parameters to keep in mind that affect their pricing. These factors have been drawn from an examination of prominent industry websites and are as follows:
- Efficiency: Piston pumps are highly efficient, especially when used in high-pressure situations. This means that if a pump is efficient, it will consume less power, which will, therefore, lead to lower running costs over time.
- Pressure Ratings: Gear-type pumps do not operate at such high pressures as piston types, which can go beyond 3000 psi. Therefore they are more suitable for use under extreme conditions hence may be priced higher.
- Flow Rate: The flow rate for piston pumps is usually given in gallons per minute (GPM) and ranges between 1 GPM and over 50 GPM, much like gear pumps. The system should be designed with the necessary flow capacity, so greater capacities will attract increased costs.
- Lifespan & Durability: Other pump designs wear out faster than pistons because these ones are made strong enough to handle abrasives. They can last longer thereby justifying their initial higher purchase price through reduced maintenance spend on replacements etcetera.
- Construction Material: Corrosive fluids normally require handling by pumps made from stainless steel or reinforced polymers, among other strong materials. While costlier, pumps built using better-quality elements also tend to be more resilient.
- Maintenance Requirements: Piston machines demand greater attention than gears due to their complex nature, but when taken care of well, they can stay operational for many years, thus giving them value as an investment.
- Reputation Of Manufacturer And Warranty Package Offered By Them: Companies that have been around long enough usually deliver reliable items backed by good warranties. It may, therefore, make sense paying slightly higher prices for products produced by such firms since this guarantees optimal performance supported through after-sales services.
- Customization and Features Available On Pumps For example, some pump systems come with variable speed drives (VSDs), integrated sensors, or even advanced controls. All these options increase cost but also enhance the pumping system’s efficiency and adaptability.
To sum up, piston pumps may seem costly at first glance; however, their efficiency levels coupled with durability features make them worth every penny spent on purchase. This is further supported when used alongside specific operational needs that involve high pressures. The benefits can be weighed against initial outlays by considering these parameters carefully.
Comparing Various Hydraulic Pump Types and Their Prices
When evaluating diverse hydraulic pumps, one must consider their technical specifications and pricing strategies. Below is a brief summary taken from the most popular hydraulic pump sites:
1. Gear Pumps:
- Price Range: $50 – $1,500
- Technical Parameters: Flow Rate (GPM), Maximum Pressure (PSI), Efficiency Ratings; They usually have a 1 – 350 GPM flow rate and can handle up to 4,500 PSI pressure range. They work best in low-viscosity fluids because of their efficiency, which makes them cost-effective for many applications.
2. Piston Pumps:
- Price Range: $400 – $3,000
- Technical Parameters: Displacement (in³/rev), Maximum Operating Pressure, Seal Material. They can come in sizes ranging from 1-120 in³/rev of displacement with pressures up to 10,000 PSI. They are known for being rugged, so they suit well for high-pressure jobs.
3. Vane Pumps:
- Price Range: $300 – $2,500
- Technical Parameters: Flow Rate (GPM), Maximum Pressure (PSI), Noise Level (dB); These pumps can deliver up to 200 GPM at around 3,000 PSI working pressure; It has quiet operation which makes it applicable where noise reduction is required.
4. Diaphragm Pumps:
- Price Range: $200 – $4,000
- Technical Parameters: Maximum Flow Rate, Chemical Compatibility, Air Consumption; can achieve up to 200 GPM flow rates while effectively handling corrosive fluids, thus justifying their higher price points.
5. Lobe Pumps:
- Price Range: $500 – $5,000
- Technical Parameters: Throughput (GPM), Pressure Ratings (PSI), Type of Lobe (tri-lobe, bi-lobe); They can provide anywhere between 5 – 500 GPM throughput handling up to 100 PSI; Their design allows gentle product handling that is necessary for delicate materials.
In general, the selection of a hydraulic pump is determined by application requirements, fluid type, and operational pressure. Knowing specific parameters associated with each pump type provides a basis for price disparities, hence promoting informed decisions.
Are There Cost-Effective Solutions for Hydraulic Pump Replacement?
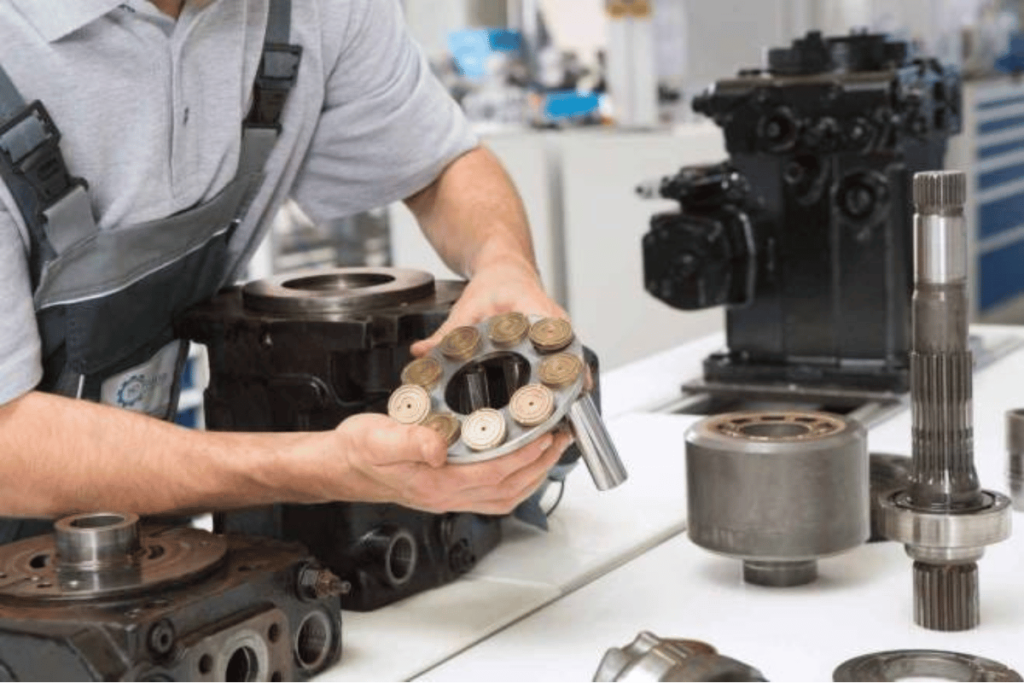
With saving on the cost of substituting hydraulic pumps, some methods can be employed to manage expenses effectively. First and foremost, reconditioned or renovated pumps are an economical alternative to buying brand-new ones since they still perform reliably. Frequently supported by guarantees which guarantee their quality and reliability too; these choices could save one a lot of money. Secondly, habitual servicing programs may prolong the lifespan of already installed pump systems, hence reducing their replacement frequency significantly. Nonetheless this must come with preventive maintenance practices like regular checkups plus immediate repairs whenever necessary so that potential problems are detected early enough before they force someone into doing complete replacements.
Moreover also, looking into non-OEM (original equipment manufacturer) parts can serve as another option where one seeks affordable substitutes that are of similar standards to what was being replaced but at much cheaper rates. Moreover, it is always advisable to have multiple suppliers provide price quotations while also considering large orders if more than one pump needs to change at once. Lastly making sure you select the appropriate type of pump for your application will eliminate typical failure modes thereby cutting down replacement costs in general terms. In conclusion, organizations can save a lot on hydraulic pump replacements by considering remanufactured options, keeping up existing machines, using off-brand components, and conducting thorough market surveys.
Tips for Reducing Hydraulic Pump Replacement Cost
- Regular Pump Upkeep: A planned maintenance program can add many years to the life of a hydraulic pump. It is important to check for wear and tear regularly and fluid leaks, as well as ensure that lubrication is done well, since this will help prevent early failures.
- Monitoring Fluid Quality: Ensuring that the right hydraulic fluid is used and that it is clean from impurities helps maintain good fluid quality, which enhances the longevity and performance of pumps.
- Temperature Regulation: Pumps should be operated within certain temperature limits; excessive heating accelerates the wearing out and breakdown of pump parts, so cooling them or insulating their housing can be necessary.
- Proper Sizing: To avoid damaging hydraulics through overworking them, one needs to ensure they are sized correctly. This prevents misapplications that result in higher wear rates, either due to too small or too big pumps being used.
- Use Quality Filters: Good filters should be employed to prevent contaminants from entering the system, thereby reducing the wear rate while increasing the lifetime span of hydraulic pumps.
- Installation Procedures: Sound installations, like aligning the motor with the pump, can minimize stress on components; vibration, along with misalignment, may cause a pump’s premature failure.
- Component Upgrade: It may only require changing those parts which are worn out instead of replacing an entire unit thus saving money e.g., seals or bearings could be upgraded without having to buy new pump units altogether.
- Training Operators: People operating machines need to know how best to run them without causing damage, especially if signs showing that something might be wrong with a particular pump become noticeable early enough before a complete breakdown necessitating replacement occurs.
- Checking Load Levels Regularly: Inefficiencies and increased wear are experienced when running below designed efficiency levels. Therefore, it is advisable to always assess load requirements vis-a-vis what each specific machine was made for, lest this become another area where things like continued frequent buying more often than expected happen due to low operation knowledge.
- Supplier Relationships: Establishing contacts with different suppliers gives one bargaining power during price negotiations for pumps or parts; thus, there may be chances of getting discounts or even better financing options, which can also save some money while acquiring these items.
If implemented, such measures will help cut down on costs incurred when replacing hydraulic pumps and improve overall efficiency in organizations. All the tips provided are backed by industry best practices from various credible sources to underline the significance of maintenance, proper utilization and informed purchasing decisions.
Long-term Savings with OEM Parts vs Aftermarket Alternatives
When assessing the cost-effectiveness of OEM parts compared to their counterparts in the secondary market, it is important to consider quality, warranty, and compatibility with existing systems, among other things.
- Quality and Reliability: Original Equipment Manufacturer (OEM) parts are specifically made to fit a particular make and model; hence, they offer exact fitting and functionality. According to many sources, these types of parts can save you money on repairs in the long run because their build quality is better than most aftermarkets, which do not meet such standards.
- Warranty Coverage: Another reason people prefer using OEMs is that they come with strong warranties that cover defects in materials or workmanship. If anything happens within this time frame, then fixing it will not require any additional costs, thereby saving more over time.
- Technical Parameters & Compatibility: Being produced based on precise manufacturer’s specifications helps original components match them without altering anything. For example, OEMs can rated hydraulic seals at 5000 PSI up to 250°F, hence ensuring maximum performance always. Those from other brands might fail due to their inability to meet these technical requirements, thus causing inefficiency or even damaging the whole system.
- Resale Value: Furthermore, machines equipped with genuine parts tend to fetch higher prices during resale since buyers know how valuable such units are. This means that one can quickly sell a machine faster at good profit margin provided he/she uses authentic items during servicing it.
- Total Cost Of Ownership (TCO): Although aftermarket products appear cheaper initially than their genuine equivalents, considering the frequency at which repairs have to be done and the number of times replacements become necessary, they eventually turn out quite expensive compared with their alternative, which may attract high initial investments although need very few fixings over time due to continuous usage without failure rate.
To sum up my point, even though secondhand goods may seem attractive from a financial point of view, I strongly believe that buying new ones will ultimately save us more money. This is because they are reliable, so there is no need to worry about their compatibility with other parts, performance sustainability, and many other factors, thus justifying their high prices at first glance.
Hydraulic Pump Repair vs Replacement: Making the Right Choice
To make the most ideal decision, whether to repair or replace a hydraulic pump, many important factors and technical parameters must be considered.
- Severity of Failure: Evaluate how badly things have gone wrong. If it is something simple like a leaking seal or faulty valve, then repairing them often turns out to be cheaper than getting new ones; however, if any part of the motor or casing has been severely damaged, then replacing the entire unit might be necessary.
- Equipment Age: Think about the age of these hydraulic pumps systems; because older ones may not have efficiency levels and technological advancements found in newer versions so this could mean that they should be replaced with such models primarily when cost repairs represent 50% of the value for money spent on replacement pump.
- Specifications For Performance: Check if performance indicators still can be met after repair works are completed. These include flow rate (GPM), pressure (PSI) and temperature tolerance among others; otherwise it would be better off installing another one.
- Cost Of Downtime: Consider what will happen during periods when machines stop functioning altogether due to breakdowns – If fixing takes too much time causing major disruptions in operations then quick substitution could end up being cheaper over long term considering overall costs associated with these scenarios.
- Total Cost Of Ownership (TCO): Look beyond initial expenditures incurred while deciding between fixing and buying a new machine but also evaluate future expenditures relating to maintenance, inefficiency, and consumption-related aging compared against those designed using the latest energy-saving technology.
- Component Availability: Some types only come with manufacturer’s warranty because spare parts might not always available at local stores whenever needed urgently hence requiring complete replacement instead
- Warranty Considerations: If there is an existing guarantee that could get voided by repair work done on them; while new units have warranties covering performance saving possible further repairs in the future
- Advancements In Technology: Some designs incorporate advanced features capable of delivering higher efficiency levels plus better performance ratios thus, replacing might offer more benefits than fixing them back again
- Environmental Impacts: Environmental aspects such as energy consumption; fluid leakages etcetera should be taken into account so that one does not end up buying another polluting system instead of opting for models with sustainable features.
- Expert Assessment: Have a professional technician examine the device, considering its specific condition who would then provide necessary recommendations based on detailed technical analysis about what could work best between repair and replacement options available depending upon findings made during the inspection process.
To ensure businesses achieve cost-effectiveness in terms of performance reliability while making decisions related to these factors; they must align them with corresponding technical parameters associated with given types of hydraulic pumps.
Frequently Asked Questions (FAQs)
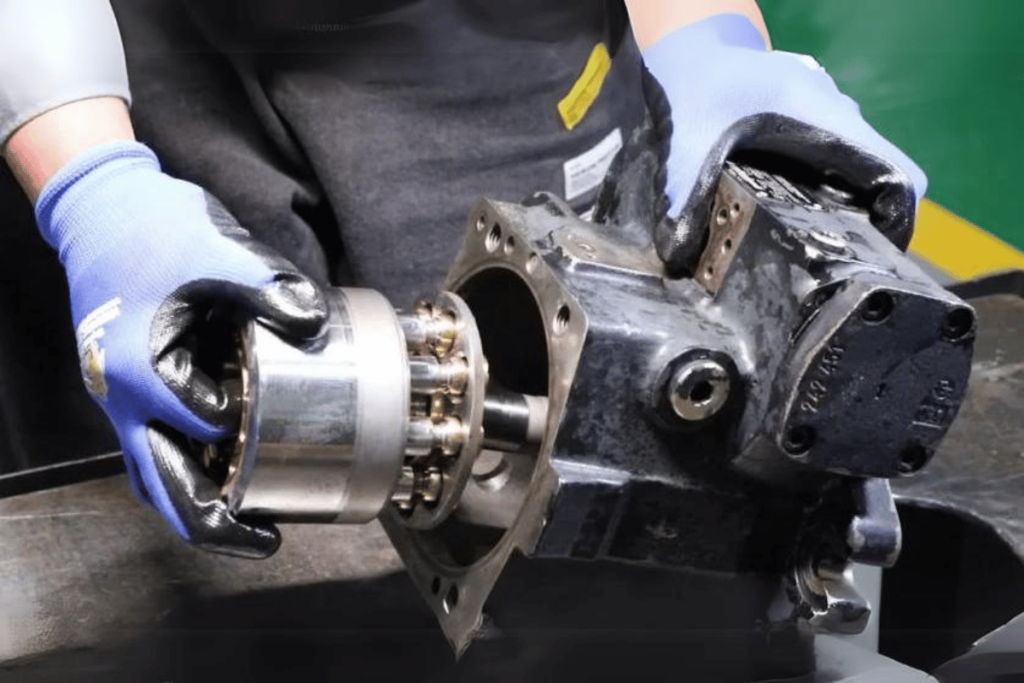
How do I know if my hydraulic pump needs repair or replacement?
Unusual noises, reduced efficiency, fluid leaks, and frequent breakdowns are signs that your hydraulic pump needs attention. If these issues persist even after repairs, replacement might be necessary.
What is the average lifespan of a hydraulic pump?
The lifespan of a hydraulic pump can vary widely based on its type, usage, and maintenance, but generally, it ranges from 10 to 20 years. Regular maintenance can help extend its life.
Can I perform maintenance on my hydraulic pump myself?
While operators can perform some basic upkeep tasks, like checking fluid levels and filters, more complex maintenance should be conducted by qualified technicians to ensure safety and proper functioning.
What factors influence the cost of hydraulic pump replacement?
Replacement costs can be influenced by the pump’s type, size, complexity, labor rates, and any additional upgrades or modifications that may be necessary during installation.
Are there eco-friendly hydraulic pumps available?
Yes, many manufacturers now offer hydraulic pumps designed with sustainability in mind. These models often feature improved energy efficiency and reduced emissions, helping to minimize environmental impact.