Hydraulic pressure control of a hydraulic pump is a crucial element in industrial applications where hydraulics is used. The performance, efficiency and reliability of the system depend on the pressure adjustments made on hydraulic pumps. A hydraulic pump’s overall efficiency relies directly on its pressure adjustment capabilities.The article gives an overview of what to expect regarding hydraulic pump pressure adjustment, why it is important and how it affects the performance of hydraulic systems. It highlights factors that influence pump settings, ways to change them, common faults to avoid as well as preferred strategies.In summary, this article aims at providing readers with an insight into hydraulic pump pressure control and its effects on the operation of the whole system. Having such information can enable companies optimize their hydraulics for better performance while reducing costs associated with running them.
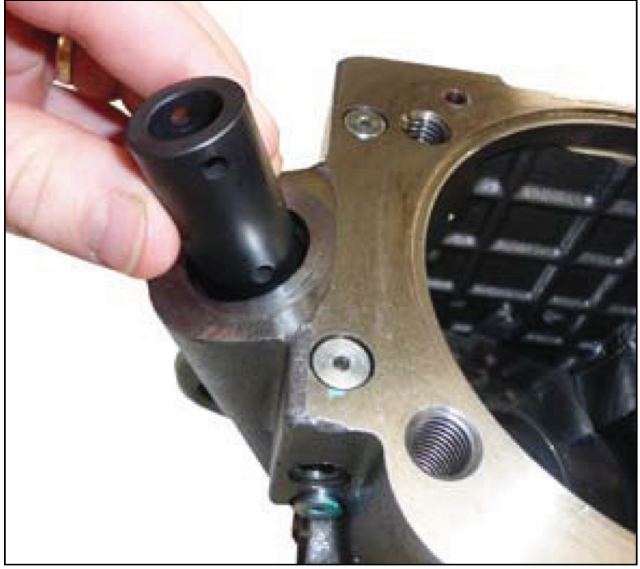
Knowing about how to adjust hydraulic pump pressure
Hydraulic pump pressure adjustment is the process of modifying the operation pressure of a hydraulic pump. It can be done in several ways, such as changing the flow rate of the hydraulic pump, adjusting its displacement or varying the pressure relief valve.
These systems have two main parts which are; pressure relief valve used in controlling maximum pressure within hydraulic system and also it has a pressure control valve that regulates flow by adjusting fluid power levels depending on what’s needed at any given time throughout this circuitry. There might be some sensors included into this setup so as to monitor automatically and keep adjusting pressures accordingly until they meet desired values for each point along the way if necessary.
What happens during hydraulic pump pressure adjustment is setting up operating pressures which affects performance all over. The best results will only be achieved when operated under right pressures while wrong ones may cause poor output with high power consumption leading even collapse through failure sometimes.
Why Proper Hydraulic Pump Pressure Adjustment is Important
Proper adjustment of pump pressures plays an integral role towards achieving optimum functionalities within hydraulic systems. When set correctly, these adjustments can help improve efficiencies thereby saving costs associated with energy use in such environments.
Moreover, machines powered by hydraulics heavily rely on them for their operations to run smoothly hence affecting machine output greatly if not done properly. In case where adjustments aren’t made accurately, machines fail to work as expected thus reducing efficiency levels drastically besides lowering productivity rates which might result into expensive downtimes eventually.
Additionally, proper hydraulic pump pressure adjustment can also contribute towards extending lifespan of various parts comprising these gadgets. Whenever settings go wrong during this process excess wear and tear take place within circuits leading towards early breakdowns of different components including valves cylinders among others mainly due to pumps failing prematurely because of incorrectness in pressures applied while using them concurrently .
In conclusion, adequate attention should always be given unto ensuring correct setup for pressures required by businesses running on machines that employ hydraulic systems. This is because failure to do so may lead not only to poor performance but also increased costs through operation optimization, machine efficiency improvement as well as reduced operating expenses.
Things that Affect the Adjustment of Hydraulic Pump Pressure
The adjustment of hydraulic pump pressure is one key element in optimizing any hydraulic system. Nevertheless, there exist numerous aspects which render the process less effective than it should be. This part will highlight all those major factors which influence adjustments in hydraulic pump pressures.
Viscosity of the fluid: The ability of a pump to create pressure when pumping can be affected by how sticky or thick its oil is. High-viscosity fluids tend to slow down flow rates through pumps thereby causing insufficient pressures at their outlets; on the other hand, low-viscosity ones may make them cavitate and this can destroy systems.
System Load: Pressure needs are dependent on what amount work has been done so far by an individual machine within a given set up. Should any machine get overloaded then obviously extra effort shall be required from all other devices thus necessitating higher pressures for proper maintenance but if they underperform due to being under-utilized premature wear and tear might occur because they have been overworked.
Type of pump employed: Another determinant capable of influencing adjustments made towards hydraulic pumps concerns their designs types or categories employed during installations where these machines are used. Each variety possesses different capabilities regarding maximum pressure achievable with some being more suitable than others especially for high-pressure applications.
Pump Size: Rate at which flow occurs as well as levels attained largely depend on sizes adopted when acquiring various components like motors among others constituting these assemblies known as systems whose function is generation forces required during operations; hence selecting small-sized options might compromise meeting target figures relating to force magnitude necessary while going for big ones could damage entire setup if not handled properly due excessive power applied.
Operating Pressure Range: Allowing values beyond limits set out within suggested ranges expected between minimums together with maximums defined by manufacturers could result into serious damages caused upon themselves including both pumps plus machinery generally speaking. In case this happens then blame rests squarely upon us since failure occurred during selection process where maximum operating pressures were exceeded or minimum ones ignored altogether.
Temperature: Performance levels linked up with adjustment measures applied towards pressure changes within hydraulic pumps cannot be achieved if fluid temperatures differ significantly from what is recommended as optimal by device makers such that either heating elements become overburdened due to excessive heat produced thereby reducing efficiency or cooling systems fail leading decreased output because cooling effect was insufficient for desired outcome.
Methods of Adjusting Hydraulic Pump Pressure.
There are a number of ways to alter hydraulic pump pressure, each with its own advantages and disadvantages. Here are some common methods that are often used:
Manual Adjustment: This method involves altering the pressure relief valve manually so as to get the required pressure. It is an uncomplicated and economical method, but it requires constant monitoring and regulation because it might fluctuate from what was set at earlier stages.
Spring Adjustment : In this case, one adjusts spring tension in the pressure relief valve to get the desired pressurization. It is not that complicated a way and demands less monitoring than manual adjustment does; however, precision may be somewhat compromised.
Pilot-Operated Relief Valve Adjustment: This type of procedure involves changing relief valve pilot pressure. It has better control for more intricate hydraulic systems whereupon the user has increased sensitivity.
Proportional Relief Valve Adjustment: This technique uses a proportional relief valve to adjust system pressures according to needs of the system. It has accurate pressure control and can be used with flow rates and loads that keep changing too often.
Load-Sensing Adjustment: The approach applies load sensing pumps as well as pressure compensators for adjusting the system’s requirements or needs by varying its pressures. With precise control over pressure, it can handle industries having different flow rates as well as loads though may need complex hydraulic systems.
Each method has its advantages and disadvantages, with what method is best for adjusting hydraulic pump pressure depending on specific hydraulic system needs.The most appropriate method should be determined by consultation with an expert in hydraulics systems for any given application.
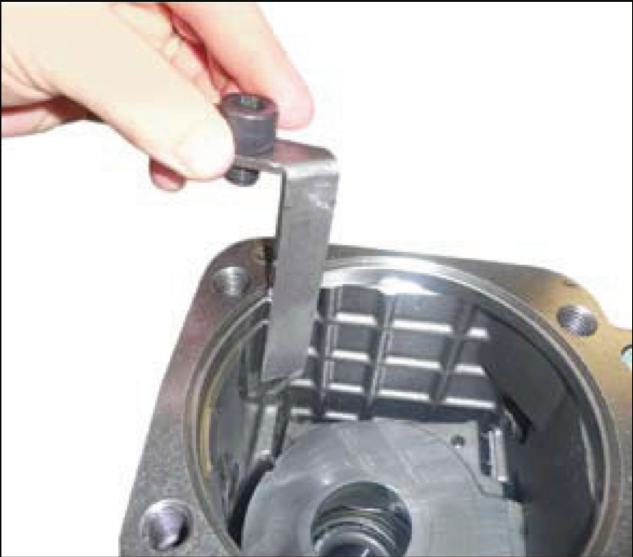
Common Errors in Setting Hydraulic Pump Pressure
Even with the most sincere intentions, mistakes can be made during hydraulic pump pressure setting. Such errors can lead to a decrease in performance and energy efficiency of the system as well as increase chances of hydraulic system failure. The following are some of the usual mistakes that people make when setting up hydraulic pump pressures:
Using incorrect hydraulic fluid: Using an unsuitable type or viscosity of hydraulic fluid can cause various problems within a hydraulic system such as reduced performance and increased wear on different parts. It is important to use appropriate hydraulics fluids recommended by respective manufacturers.
Failure to set the pressure at right level: If you do not set your hydraulic pump’s pressure at correct level, then it might fail to work as expected. This means that its output will be inefficient resulting into low power consumption by machines hence high electricity bills besides wearing out quickly due increased friction between moving surfaces.
Ignoring load characteristics: Load characteristics should always be considered whenever one is adjusting his/her hydraulics pumps’ pressures because failure to do so may result into poor performance or even breakdowns within these systems.
Over-adjusting pressure: Over-adjustment may damage parts like seals and decrease overall efficiency among other things like lessening useful life thereby leading to poor system functioning over time which could have been avoided if only required levels were adhered to initially according recommendations given by manufacturer(s) concerned…..
Neglecting proper maintenance: Poor maintenance practices such as allowing leaks occur or contaminating whole setup during servicing can greatly affect how well one performs adjustments related with this kind of equipment used for industrial production purposes. It is therefore necessary that regular checks ups are done coupled with appropriate servicing procedures observed all times without fail so that such issues do not arise.
Incorrect installation methods: In case any particular component fails work upon being fitted wrongly then it becomes impossible achieve desired results regarding setting up correct values associated with operating pressures required from various devices comprising part or complete assembly which forms portion of such systems used within factories etcetera where they are installed. Therefore, should make sure follow manufacturer’s instructions carefully when installing hydraulic components….
Failure to check performance after making changes: It is important monitoring system performance especially after effecting modifications aimed at enhancing efficiency levels as well ensuring everything functions according expectations set by individuals involved in these processes but mostly managers who rely greatly on them for smooth running their organizations etcetera.
To avoid the above mentioned common errors one has to follow proper procedure while trying adjust any hydraulic pump pressure and also keep in mind what manufacturers say about this matter. Moreover regular servicing should be carried out coupled with continuous evaluation so as detect problems earlier before they become bigger thus jeopardizing productivity levels attained within production plants or any other place where such machinery may be employed.
Hydraulic Pump Pressure Adjustment Superlative Tactics
For the efficient functioning of hydraulic systems, proper hydraulic pump pressure adjustment is necessary. To achieve this there are some best practices that should be followed so as to optimize performance and extend the life of the machine. Below are some tips on how to adjust a hydraulic pump’s pressure:
Adhere to Manufacturer’s Instructions: Following instructions given by manufacturers when adjusting pressures in hydraulic pumps is vital. This is because each type of these devices has its own peculiarities in terms of operation; failure to observe such can lead to inefficiency during use or even breakdown.
Keep an Eye on System Pressure: When setting up for adjustments in pump pressure it is crucial that one constantly keeps track of the general system’s pressure. Failure which may mean having ranges beyond safe working conditions thus causing harm or damage.
Use Right Tools: During adjustment processes various tools must be used if accuracy needs to be achieved while making measurements as well as effecting changes within our hydraulics systems.
Take Small Steps: Instead of making drastic alterations at once, it is advisable that you change slowly inch by inch until desired results are realized with regard to our hydraulics’ oil pumping mechanism.Instantaneous modifications can destroy their parts leading them not work properly or stop altogether.
Carry Out Regular Inspections: Whenever there seems something unusual about your machine try looking into what might have gone wrong especially related aspects like checking whether there been any failure due too much/less pressure being exerted upon them over time besides other components associated with such failures showing signs too much stress exerted over periods .
Think Long-term: Frequently servicing these apparatuses helps us detect faults early enough before they become more complex thus saving money through repairs and replacements which could have been avoided had we taken care better off them earlier during maintenance checks concerning adjusting their forces for pumping oils.
Put Safety First: The most important thing while doing anything connected with altering limits within these devices that should be considered paramount at all times is safety.Security precautions must strictly observed so that accidents do not occur during this process.
Conclusion
In conclusion, optimal performance and efficiency of the hydraulic system require appropriate pressure regulation of the hydraulic pump. A finely-tuned hydraulic pump ensures that the hydraulics work efficiently, which in turn leads to better machine productivity and reduced energy consumption.
The article explicates on the meaning and components of hydraulic pump pressure adjustment as well as its importance and benefits in industrial applications. Furthermore, we have explored factors affecting hydraulic pump pressure adjustment; ways of adjusting hydraulic pump pressure; and common mistakes to avoid when doing this process. Additionally, we gave recommended best practices for successful hydraulic pump pressure adjustment, maintenance.
Therefore, it is important for businesses to understand that if such adjustments are not properly made then some major consequences might be experienced including poor machines performance; high energy consumption rates; premature equipment failure among others. To this end, firms need to assign priority to correct adjustments of their hydraulic pumps in line with the optimization of their systems for optimum efficiency and effectiveness.
As technology continues to advance, we can expect future trends in terms of improvement regarding the overall system performance and energy efficiency through the process of hydraulic pump pressure adjustment. However, it is necessary for companies not only keeping in touch with best practices but also following industry developments so as to remain competitive while being efficient in their operations.
In conclusion , proper consideration should be given on proper hydrolic pump presure adjustent by businesses as a vital part of their strategies towards optimising these units. When industries or companies do adopt such practices they will be sure they will achieve goals like improved machine performance levels requiring less consumption on energy as well as long use life cycle by avoiding common mistakes or following all steps outlined by experts in order that they receive higher returns within a short period of time..