What are the ways of adjusting hydraulic pump pressure? In hydraulic systems, the right adjustment of hydraulic pump pressure is important for system performance and competence. A lot of situations require manual adjustment of hydraulic pump pressure as compared to automatic where it is not possible or when the system requirements change. Therefore, one should know how to manually regulate a hydraulic pump pressure for maintaining its functionality.Hydraulic systems are commonly used in diverse industrial applications such as manufacturing, construction, and transportation. In these cases, the hydraulic pumps provide force and motion needed to operate various components like valves, motors and cylinders. Consequently, maintaining correct levels of hydraulic pump pressure is necessary in order to improve performance and efficiency.
What this article does is that it offers a step by step guide on how you can use technology to adjust your pump’s operating parameters manually. The article will discuss why it is important for individuals to understand how to adjust their own pumps’ pressures; the stages that are followed while making adjustments on a manual basis; evaluating whether your pumping machine meets required specifications; precautionary measures which need consideration during this process and finally benefits that come with proper alteration of pressures on hydrostatic systems.By the end of this article,you will get an insight on how you can undertake manual adjustments on your pumping unit.
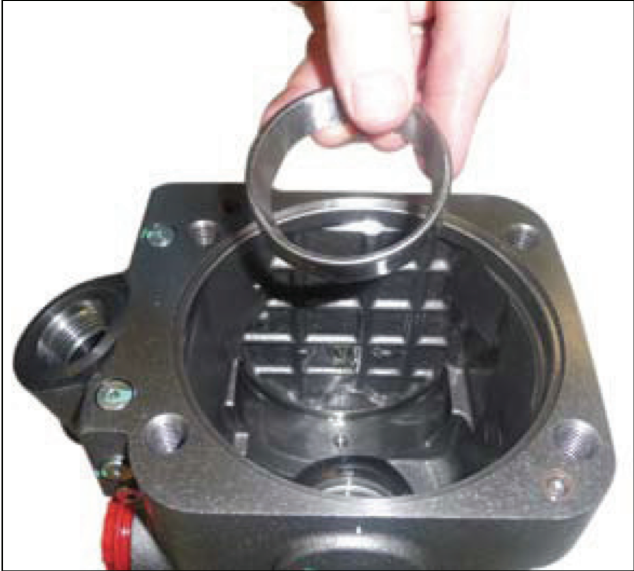
Understanding Pressure Adjustment of a Hydraulic Pump
To ensure that hydraulic systems are functioning properly, it is important to understand how to adjust the pressure of a hydraulic pump. The overall performance of any given hydraulic system is heavily influenced by its pressure levels among other things. Some of the reasons why adjustments may be necessary include optimization and maintain equipment efficiency as well as meeting operational requirements.
Hydraulic pump pressure adjustment refers to altering pressure levels within a hydraulic system through changing settings on an associated pumps. Such types generate power for various components in terms of hydraulic energy which can be used elsewhere or stored until required again later in time as explained before somewhere here already written words this sentence too long maybe I should stop now but then again while I’m at it might just keep going forever until someone tells me not too anymore than what was said here already given information once more over and over again always saying same thing repeatedly no matter what happens next after all we have nothing better do with our lives than read these instructions prompts for creativity so let us continue on shall we?
Effective adjustment necessitates understanding the different parts that make up this process. The four main elements are; gauge relief valve control valve pump Whereby; A gauge shows how much force has been applied by measuring changes (increase/decrease) in units such as kilopascals or pounds per square inch PSI . This information could also help one know when there’s need for adjustment based on readings obtained from other sources like flowmeters which measure quantity an amount flowing past certain point within specified period time taken otherwise known as liters / minute LPM . Relief valves are designed to open automatically once set maximum limit has been reached thus ensuring protection against damage due excessive pressures , The direction flow can be regulated using either manually operated valves (by hand) or automated ones (using electricity).
Hydraulic pump pressure adjustment involves making changes to the hydraulic system’s pressure levels by adjusting the hydraulic pump. What this means is that a person would need to alter settings on an associated pumps thereby increasing or decreasing amount of power being generated for different components in form energy which could be used elsewhere or saved until it becomes necessary once again later sometime during future. Depending on design and requirements, these may be done manually or automatically controlled with some types having ability adjust themselves continuously according certain range values beyond which they cannot go further unless reset by user .
Why adjust hydraulic pump pressure manually?
The pressure of the hydraulic fluid is the most important thing in hydraulic systems as it determines how well they work. The hydraulic pump creates this necessary force for driving the whole system; thus fluctuations could lead to performance problems or even damage it. Situations may arise when it becomes necessary to change the hydraulic pump pressure manually either for optimum performance achievement or adapting with new conditions.
There are various reasons why one should opt for manual adjustment rather than automatic adjustments on their pumps’ pressures. Firstly, you can fine-tune your machines by adjusting little levels of force using hands only unlike when using automated devices which detect major shifts only but not slight changes caused by loads variations within systems thereby leading to underperformance of such mechanisms. Secondly, there can be times where automatic pressure relief valves would fail to function due absence or breakdown hence making us rely on our ability adjust it ourselves so that things continue working fine as expected.
One should know that manual adjustment is different from automatic adjustment since with manual one has to do physical work by setting values directly onto controls while in automatics all these things happen electronically without any human intervention at all thus requiring knowledge about what each button does and following right steps otherwise harm could occur either equipment being used or user itself.
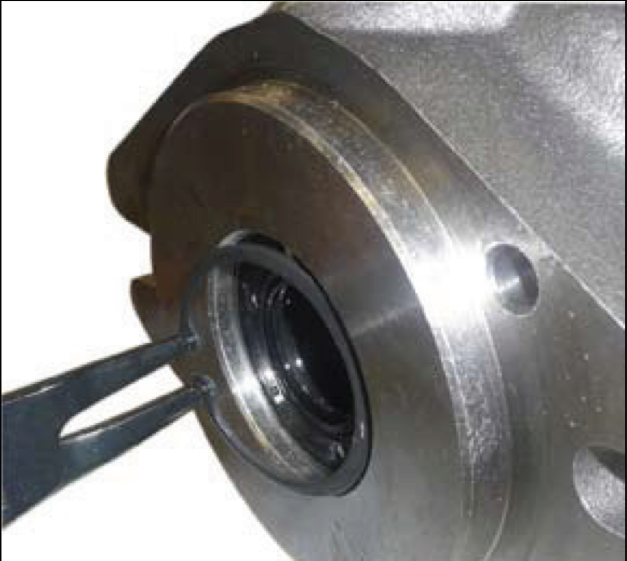
How to Adjust Hydraulic Pump Pressure Manually.
A number of preparatory measures need to be carried out when adjusting hydraulic pump pressures manually so as to ensure that this adjustment is done smoothly and safely. Here are the steps you can follow:
Locate the hydraulic pump: Before setting the hydraulic pump pressure, locate the pump and find where pressure adjustment can be made. Typically it’s a pressure relief valve close to the pump.
Inspect system pressure: Measure your current system pressure before attempting to adjust its hydraulic pump pressure. This will act as a reference point for the required level of pressurization.
Reduce system pressure: You should release all systems pressures first before doing any adjustments so as not put yourself in danger of accidents. Either open up your hydraulic valve or operate on your hydraulics.
Remove protective cap: For better access, there will always be a cover on top of the unit covering the means for regulating its temperature.
Use a gauge for measuring pressures: When you adjust that mechanism, attach a gauge that will measure the force applied by it during this process; this will enable you regulate more accurately that force desired.
Twist pressure adjusting screw: The screw which directs how much force flows through inside an engine is called a “pressure adjusting screw”. Just use such instruments as a screw driver or others like that have been mentioned above to increase or decrease according to one’s wish.
Monitor indicator of compressing forces applying into engines: While turning you may notice different indicators being changed, especially while moving in one direction up or down towards its target value so never try over adjustments leading devices’ damages due wrong corrections made too far at once time
Prevent pressurized fluid from escaping The moment necessary strain has been achieved; further actions can only work against desired results hence call for locking such screws with nuts having features similar to those found on locks
Assess System Pressure again Finally, check if system monitoring readings have reached required value. Otherwise, you should make some more modifications until the desirable pressure is achieved.
It should be noted that those were general instructions and specific instructions may vary depending on the type of hydraulic pump being used and the kind of hydraulic system being run. It is also important to observe all safety guidelines and use appropriate personal protective equipment when making these adjustments.
Process of Setting Hydraulic Pump Pressure
To set the desired pump pressure, you can start by adjusting the pump manually. Carry out the following activities:
Find the pressure adjustment valve: The position of this valve would depend on either on the pump or elsewhere in the hydraulic system, depending on which type of hydraulic pump is installed. To find it please consult either a manual for a pump or schematics of a system.
Check current pressure setting: Use a pressure gauge to ascertain what is currently set for pressure. This will serve as a reference for setting the new value.
Adjusting Pressure: With this, use your adjustment valve to increase or decrease your required force. For an increment in force turn it clockwise while for reduction in force turn it anti-clockwise and in small increments test it until it fits your requirement up to that specific level
Pressure gauge check: After these changes, ensure that you look at your pressure gauge to see if you really got the desired outcome. If not, continue with small adjustments until you get what you want.
Locking adjustment valves: Once you have achieved this perfect level of pressure, lock down those valves so as not to tamper with them again.
New recorded readings are written for future intentions.
It’s important to note that every hydraulic pump is different and therefore certain variations may exist depending on its make or model as pertaining to pressure adjustment procedures. Always refer to your pumping machine’s user manual and follow through their instructions concerning these matters concerning changing pressures. Also it important that when testing one ensures correct calibration and accuracy of Pressure Gauges being used since if faulty they might lead into wrong values which could result into unsafe performance from fluid power systems.
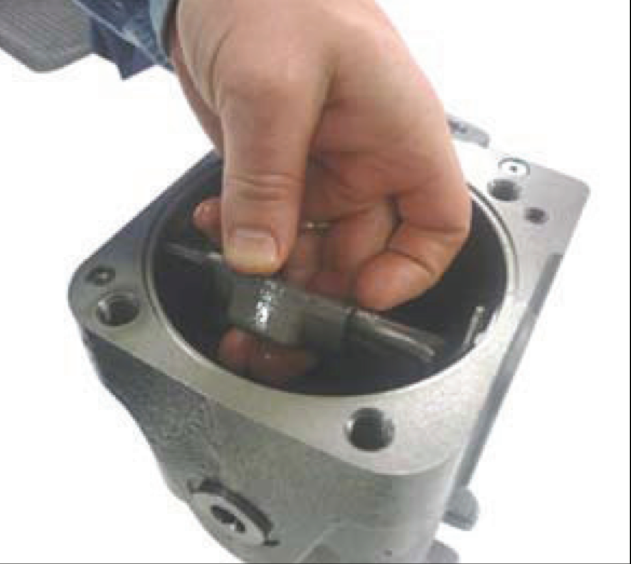
Testing the performance of hydraulic pumps
After manually adjusting hydraulic pump pressure, it becomes necessary to test its efficiency and this can be done by carrying out several tests which can ascertain this.
The first test to be performed is flow rate test. This test checks if the hydraulic pump produces adequate flow rate for the system. There are many ways in which a person can tell whether or not a particular hydraulic pump is functioning optimally and one of these methods involves testing its flow rate. Generally speaking, all hydraulic systems require power input but where this comes from depends on what type of machines are being used as well as their sizes or functions within industries.
The second test that should be conducted is a pressure test. A pressure gauge should be attached at the outlet side of the pump then operated at required speed to measure the amount produced by it in order to ensure that this falls within limits set by manufacturer’s recommendations otherwise adjustments may need to be made on pressures applied towards different ends such as inlet or outlet sides where necessary until desired results can only achieved through changing settings like increasing / decreasing values accordingly until they match up with what was intended initially during design stage itself so-called “range” statement refers back here.
Thirdly, there must also exist temperature tests which determine whether given fluid meets required ranges. With respect to hydraulic systems, temperature regulations need adherence just like any other industry would require control over its heating ventilation and air conditioning system (HVAC). When monitoring temperatures inside an enclosure containing fluids used for driving motors requiring frequent stop starts due continuous load fluctuations caused by intermittent connections between them then it becomes apparent that there is need for such kind of check-up especially when ambient condition changes rapidly over short periods because failure may result into breakdown thus affecting smooth running process altogether besides interfering with overall efficiency levels maintained during operations carried out within these areas including both outdoor and indoor activities alike.
It is therefore important that regular assessments are made after performance testing so as not only identify but also resolve any problems with the pump. Once this is done and found to be in good working order then it can safely be put back into service immediately; however if adjustments have been made during subsequent retests and are still required while expecting desired results from them then another series of performance tests should follow until all necessary changes have been accomplished where after only necessary adjustments may need to take place again which could include manual changes done on pressure settings until required levels are attained by the device itself.
In addition to checking the operation of a hydraulic pump, there is need for regular monitoring so as keep track of its functions at different stages. These stages may involve pumping stations located along pipelines or even within reservoirs themselves where inspection could be carried out periodically with possible maintenance being undertaken as part of routine checks aimed at ensuring smooth running operations achieved throughout an entire system that utilizes such types of equipment among others.
Concerns about safety when you manually adjust hydraulic pump pressure
It is important to ensure that all precautions are taken into account so as to prevent accidents or injuries while working on hydraulic systems. As we all know, hydraulic systems work under high pressure which may result into severe injuries or even death if mishandled. The following are some of the things that should be observed to enhance safety during manual adjustment of hydralic pump pressure:
Put on the right personal protective equipment (PPE): Workers must wear suitable PPE such as safety glasses, gloves and steel-toed boots before they start operating any machinery related with hydraulics. This gear will help them a lot in preventing such kind of injuries assuming anything goes wrong.
Relieve the pressure: Another thing you need to take care about is releasing off all pressures from your system prior making any changes in it hydraulically operated parts. You can always switch off this machine then open bleed valve so that any trapped air can escape through there thus relieving excess force within it.
Use correct tools: When adjusting pump’s PSI do not use improper tools which were not designed for such kind of work otherwise accident may occur due to their inability withstand much higher pressures involved here.
Never check for leaks with body parts: Moreover, never use your own body parts when looking for leakages within those areas connected by hoses carrying fluids under tremendous forces because if something happens unfortunately one might lose his/her hand forever among other bad things like death.
Adhere to standard practices: Always stick with recommended steps for modifying levels of fluid power outputted by these devices; always ensure that you have depressurized whole system, used appropriate tooling and checked everything after doing alterations.
Training: It is also very important to train people who operate machines driven by fluids on how best they can reduce or increase the amount of energy transferred at any given time through them safely without causing harm either themselves or others around especially when doing any adjustment manually.
Maintain your system: Finally, carry out regular check-ups on hydraulics in order to ensure that all parts are functioning properly which will greatly minimize risks associated with operating them.
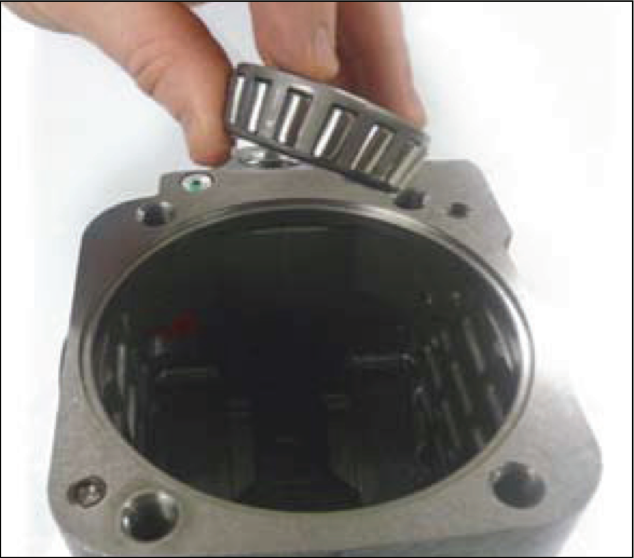
Conclusion
Aside from the obvious, fine hydraulic pump pressure adjustment is essential for smooth hydraulic system operation. You can manually adjust hydraulic pump pressure to optimize the system for specific purposes, and this will increase its energy efficiency while minimising probable instances of equipment failing. In this article we have given a step-by-step guide on how to manually adjust hydraulic pump pressure; however it should be noted that only trained personnel should perform such adjustments.
In conclusion, it is vital that companies using hydraulic systems acquaint themselves with how to manually adjust hydraulic pump pressure. This article outlines some steps that one could follow as well as safety precautions which must be observed in order to ensure optimal performance of your hydraulics. By doing so, businesses can minimize their maintenance costs, extend the lifespan of their equipment and increase their productivity. Consequently businesses are called upon to train their workforce on manual hydraulic pump pressure adjustment and incorporate it in their maintenance as well as optimization programs.