In the last few years, pressure compensated hydraulic pumps have been increasingly valued in the hydraulic industry for their capability to maintain constant pressure regardless of flow demand variations. The result has been significant improvements in hydraulic system performance effectiveness and reliability. Pressure compensated hydraulic pumps are today a must have component for industries when looking to better their processes.This article presents an insight into the latest developments regarding pressure compensated hydraulic pumps that impact on hydraulic systems. We shall examine why this is a relevant topic in industrial applications and give an overview of some of the key features and advantages that come with these latest advancements. This document seeks to offer readers a comprehensive understanding about progress made in advanced pressure-compensated hydraulic pumps use towards optimum performance in hydro systems.

Comprehending Pressure-Compensated Hydraulic Pumps
Pressure-compensated hydraulic pumps are a type of hydraulic pump that adjusts automatically to keep up a continuous output pressure. This is accomplished through employing a compensator which balances the displacement of the pump with regards to modifications in system pressure.
The displacement of the pump refers to how much fluid power per revolution or cycle is produced as it moves. By making changes to this volume basing on pressures, such pumps can deliver constant flow rate despite any shift in demand for pressure across the system.
There are two main ways that these kinds of machines can be operated; namely: pressure compensated flow control mode and pressure compensated pressure control mode. In the former, what happens is that while trying its best not let out too much oil too fast (maintain constant rate), if let say something suddenly blocks all outlets but one then this device will have no otherwise other than increasing its size so as still has same amount flowing through each path at every instant also known as keeping them parallel). The latter is quite different because here even though we want always having some specific force acting upon an object irrespective whether there were changes or not elsewhere – it must remain unchanged throughout.
There are many benefits associated with the use of these types of devices. One significant advantage is that they ensure uniformity in flow rate even when there are variations in demand for system pressures. This guarantees maximum efficiency levels while preventing damages caused by fluctuations in pressure.
Another advantage is their energy-saving nature which comes about due to maintaining constant flow rates thereby reducing energy consumption as well as operating costs involved during pumping activities done by machines using this technology. Additionally, service life span can be extended because wear and tear effects on pumps alongside other components within hydraulic systems may reduce since adjustments take place automatically depending on need thus minimizing maintenance requirements too.
Newest Advances in Pressure Compensated Hydraulic Pumps
Many breakthroughs have been made in the field of pressure compensated hydraulic pumps. These discoveries are centered on enhancing the performance, dependability and efficiency of hydraulic systems.
For instance, electronic control technology has recently been integrated into pressure-compensated hydraulic pumps. Through this innovation, hydraulics are able to alter pump flow and pressure automatically so as to optimize real time system performance. Because of these changes, hydraulic systems have become more efficient as well as reliable while still remaining safe.
Variable displacement pump technology is another new development in this area. By allowing alteration of pump displacement so that it can always remain at a constant level even when load conditions change; variable displacement pumps make hydraulic systems adaptable to such changes thus saving energy at the same time. This means that they are able to adjust themselves according to different loads unlike before when they could only work under one specific condition throughout their operation life cycle which was not economical nor sustainable in terms of power consumption.
Moreover, materials like high-strength aluminum alloys are now being used during manufacture process of pressure compensated hydraulic pumps instead of using traditional ones such as cast iron or steel . The reason behind this choice is because these new materials possess better properties than those old ones hence leading to increased strength and longer service life for hydraulics.
Lastly, software programs together with monitoring systems have come up with improved diagnostic capabilities coupled with predictive maintenance features for pressure compensated hydraulic pumps. These diagnostic tools enable faster identification of failures within such devices through which necessary steps can be taken quickly without wasting much time or resources thus reducing downtime hours thereby increasing productivity levels within organizations dealing with heavy duty machinery reliant on hydraulics for operation success.
In summary; recent advancements made towards pressure compensating technology applied within various types of hydrostatic machines working under different loads show significant achievement not only in terms of overall performance but also reliability enhancement where some components were designed specifically based on expected working conditions.
Pressure-Compensated Hydraulic Pumps: Applications
Pressure-compensated hydraulic pumps are widely used in different industries such as construction, manufacturing, agriculture and transportation; these types of pumps are suitable for applications requiring accuracy in hydraulic pressure and flow rate control.
Heavy machinery is one area where pressure-compensated hydraulic pumps are commonly applied. For example, excavators, loaders and bulldozers fall under this category of machinery which rely on strong hydraulic systems to perform duties such as digging, lifting and dragging heavy loads. Pressure-compensated hydraulic pumps offer the required power and precision that enable them to carry out these duties effectively.
Manufacturing processes also tend to use this type of pump often. Most production procedures require careful control of hydraulic pressure and flow rates. This level of control can be achieved through using pressure-compensated hydraulic pumps to enhance efficiency and productivity within the manufacturing industry.
In agriculture, pressure compensated hydraulic pumps form part of equipment like tractors, harvesters or sprayers. They are utilized to propel hydraulics that do ploughing planting or harvesting among other tasks. The presence of precision coupled with control assured by the use of pressurized compensated hydraulic pump ensures completion of these activities effectively.
Trucks busses among other means use hydrostatic transmissions with their brakes steering etc being powered by pressure compensatesd hydralic pump .Precision as well as control given by a set of force applying mechanism in terms compensatedx pumos makes it safe therefore ensuring good performance .
Various factors such as specific application requirements, operating conditions, and performance criteria ought to be considered when selecting an installing a pressure compensated hydraulic pump.Collaborating with a specialist supplier for hydraulics would play a significant role in choosing an appropriate pump capable performing its roles effectively.
Numerous case studies have shown that industrial machinery can be operated more efficiently after installing a pressure compensated hydraulic pump leading to lower downtime ,improved efficiency ,and better performance as a result. Therefore corporations can enhance their hydraulic systems by adopting the latest pressure-compensated hydraulic pump technologies.
Trends of the Future in Pressure-Compensated Hydraulic Pumps
The hydraulic industry is continuously changing, and pressure compensated hydraulic pumps are not left behind. In recent times, pressure-compensated hydraulic pumps have witnessed considerable improvements and these advancements set the stage for future trends.
An important trend among others that can be mentioned about this technology is its efficiency in terms of energy used and saved. The global effort to reduce greenhouse gas emissions by industries has pushed for even more efficient hydraulic systems. Some new developments include electronic controls which help save power where it is not needed or variable displacement technology designed to optimize energy consumption while minimizing wastage with regards to pressure compensated hydraulic pumps.
Another rising trend concerning these types of machines involves their connection abilities through smart technologies integration into them over time as we know them now. With an increased awareness on IoT (Internet Of Things), hydraulics are becoming interconnected such that never before seen Real Time Monitoring capability is achieved within smart pressure compensating pump itself that allows adjustment during operation based on current readings thereby giving users maximum control over their systems efficiency like never before possible.
Lastly, but not least there has been a growing demand for versatility and adaptability when it comes to designing pressure compensated hydraulic pumps meant for different industries; this being so because many sectors have unique specifications regarding what they require from such systems thus making customization increasingly important than ever before in history. Technological advances in manufacturing process coupled with innovative designs have made it easier for engineers to create tailor made products which can address diverse needs within various industrial settings using components available at hand without necessarily having expensive tooling done.
What remains certain throughout all these changes happening around us today within our own backyard too as far away places across oceans deep blue sea salt air breezes blowing gentle whispers carried away wind currents dusty deserts arid sun scorched plains endless rolling hills verdant fields lush forests dark jungles teeming life unseen underfoot wetlands marshy swamps still waters calm lakes raging rivers cascading waterfalls majestic mountains snow-capped peaks dry brittle tundra frozen north starry night skies sparkling with countless stars galaxies beyond comprehension universes without end — is that pressure compensated hydraulic pumps will continue to be invaluable in future years of industrial growth due its ability deliver high performance coupled with energy efficiency while becoming even more customizable along the way as connectivity increases further into this century and beyond.
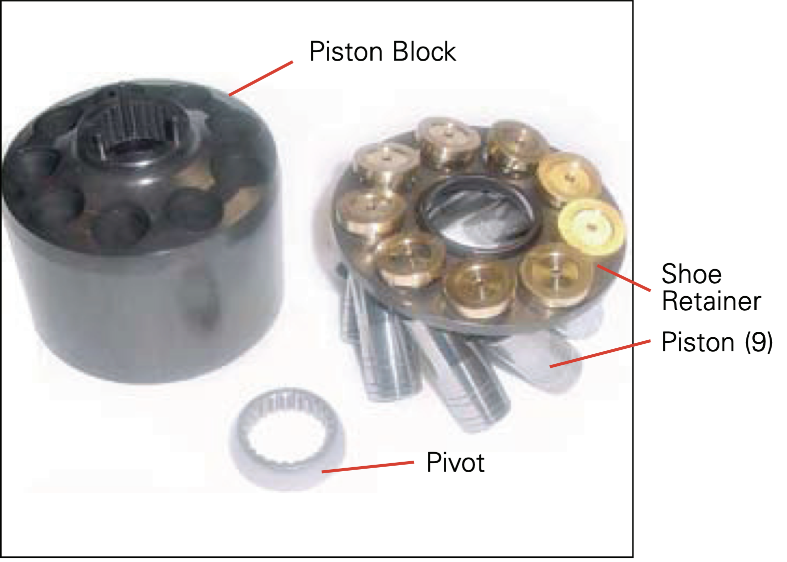
Limitations and Difficulties of Pressure-Compensated Hydraulic Pumps
Pressure-compensated hydraulic pumps are much better than their traditional counterparts but they have limitations too! Knowing these difficulties is necessary for selecting and deploying them in industrial settings. Here we will talk about some common problems associated with pressure compensated hydraulic pumps.
Restricted range of flow: The flow of pressure-compensated pumps can only occur within a certain limit which is usually limited. Therefore, this may be a big drawback in some applications where the demand for fluid is higher than what the machine can supply at any given time. Consequently, such systems become unstable when fluid demand exceeds maximum pump output leading to low performance due to lower pressure.
Expensive: Generally speaking, compared with conventional counterparts, pressure compensated hydraulic pumps tend to be more costly. This might pose an issue especially to small businesses that have tight financial constraints but it should not because its efficiency levels are better hence saving on energy cost over time.
Viscosity Sensitivity: Varying degrees of thickness affect pressure compensation capability of hydraulic machines since they react differently according to this property too; therefore if there were changes in viscosity then maintaining constant pressures by such equipment would be difficult thereby resulting into poor performance agains system requirements.
Complexity: Unlike ordinary machines used alongside these gadgets come equipped with additional components as well controls plus other things making them quite complex compared against traditional types also requiring more care during installation stage besides regular maintenance thereafter otherwise everything will fall apart sooner rather than later!
Heat Generation: When operated under high temperatures environments like those encountered at industries or factories working conditions may greatly reduce service life span before failure occurs owing mainly due too excessive heat generated through mechanical friction between moving parts within the machine itself including bearings seals etcetera thus causing premature breakdowns hence need frequent replacement parts which are expensive affairs indeed .
Cavitation tendency – Cavitations occurs when the fluid’s vapor pressure exceeds its ambient value i.e., where bubbles form and collapse, releasing energy that can damage adjacent surfaces. Such a thing is more likely to take place with pressure compensated hydraulic pumps than their ordinary counterparts.
Noise: In comparison with normal ones; the noise level produced by pressure-compensated hydraulic pump systems is usually higher which could pose problems especially in those areas where silence should be maintained such as residential estates or hospitals among others.
Nevertheless, despite these limitations and difficulties, there are many more advantages for using this type of machines over conventional ones so understanding them will enable one use them correctly thus ensuring better overall performance. The next segment will discuss recommended preventive maintenance measures for these types of pumps.
Pressure-Compensated Hydraulic Pumps Maintenance and Troubleshooting
The continuous performance and long-life sustainability of pressure-compensated hydraulic pumps can only be sustained through proper maintenance. Other topics to be covered in this section are recommended maintenance practices, troubleshooting techniques and tips for optimizing the performance of a pressure-compensated hydraulic pump.
Recommended maintenance practices
Consesquently, regular maintenance is important in ensuring that pressure-compensated hydraulic pumps operate efficiently as well as effectively. Some of these include:
Keep the fluid clean and at correct level: The fluid which is used in hydraulics can get contaminated over time leading to its poor performance and even damage to the respective pump. It should be kept clean by changing it regularly whenever needed. Additionally, it must have a specific level so as to prevent cavitation among others.
Check the pump often: This will help identify any potential issues before they become serious. It involves checking for leakages, loose connections or worn out parts.
Spare no effort on replacing filters and other components: Filters do most of the work when it comes to cleaning hydraulic fluids because they remove all contaminants from them. Filter replacement ensures that the machine keeps running at optimum efficiency while other items like Hoses, Seals and O-Rings might need their replacements done too.
Adhere strictly to manufacturer’s instructions during servicing: Normally manufacturers provide guidelines on keeping up with their pressure compensated hydraulic pumps. These instructions should always be followed so as not to void any warranties that may exist.
Troubleshooting techniques
When there are problems with a pressure-compensated hydraulic pump, these tests can help one ascertain what has gone wrong and how best one can respond to such an eventuality. Some common troubleshooting techniques include:
Leaks checkup: Leaks could mean that there would be poor performance by the pump itself or worse still; cause damage upon discovering them within a given system such as hoses connected with others.
Fluid levels and condition check-up: It has been made clear that the cleanliness and level of hydraulic fluid are to be strictly maintained for proper functioning of any pump. Hence, checking up on the levels as well as the condition can bring forth some possible problems.
Blockages inquiry: Captured in hoses or filters, blockages might result into poor performance which may possibly interfere with the functionality of a pump.
Damage inspection: As a matter of fact, parts tend to wear or get damaged over time which consequently leads to poor performance and sometimes failure. So inspecting them for damage is a good way of solving these issues.
Tips for optimizing pressure-compensated hydraulic pump performance
Finally, regular maintenance and troubleshooting can be complemented by the following tips on optimizing pressure-compensated hydraulic pump performance:
Make sure that the right size pump is used: For instance; it must be well understood that an undersized one may not enable an optimum operation while an oversized one would only lead to wastage among other negative effects.
Ensure correct installation of pumps: A proper alignment, correct fluid levels, adequate hose configurations along with fitting installations require immediate attention in order to achieve optimal performances from pumps.
Performance monitoring activities should also be put in place: Checking such parameters as fluid levels, pressure and temperature will help identify what could have gone wrong at earlier stages before things get out hand.
Appreciate environmental factors: The environment within which the pump operates plays a role in its output. High temperatures or contact with impurities can reduce its effectiveness or even cause it harm.
The maintenance process, troubleshooting tips and optimization suggestions mentioned here should be followed for so that they can make sure that pressure compensated hydraulic pumps are as efficient as possible and continue to provide reliable service through their lifetime.
Conclusion
In conclusion, pressure-compensated hydraulic pumps are an important part of hydraulic systems and this is why their further development is necessary for the growth of the hydraulic industry. The new designs in pressure-compensated hydraulic pumps have allowed hydraulic systems to operate with higher efficiencies while consuming less energy and working at increased productivity levels.
Pressure compensated hydraulic pumps have many advantages that make them suitable for different applications due to their ability to keep flow rate constant without alteration under changing loads. Among various industries such as manufacturing plants, construction companies, agricultural sector or those involved in aerospace, pressure compensated hydraulic pumps play a major role.
Emerging trends indicate that the future of pressure-compensated hydraulic pumps will be characterized by enhancing their performance, improving their durability and limiting environment impacts. Pressure-compensated hydraulics will continue playing an important role in making sure these complex systems work properly.
To achieve better performance, lower energy consumption and improved productivity resulting into significant cost savings businesses using hydraulics should consider integrating the latest models of pressure compensated hydraulic pump systems.
In brief, in the future, there could be no advancing hydraulic systems without further development of one crucial technology that will continuously redefine the whole concept of hydraulics, and it’s rather called as Pressure-Compensated Hydraulic Pumps (PCHPs).