Hydraulic control systems consist of hydraulic compensator valves, which are necessary in regulating the flow and pressure of fluid. These valves assist in ensuring the efficiency and effectiveness of hydraulic systems. We will delve into the definition and purpose of hydraulic compensator valves, their historical background, and also give an outline on hydraulic control systems.
Definition and Function of Hydraulic Compensator Valves This is a device that helps regulate fluid flow and pressure in a hydraulic system. It does this by modifying the size of the valve opening to control how much fluid can be passed through it. The major use for the valve is to make sure that any change in either load or flow results in a steady pressure of liquid within the system.
Historical Background of Hydraulic Compensator Valves As early as 1930s several companies claimed patent rights for hydraulic compensator valves while others had them way back from 1900s during the inception of hydraulics.
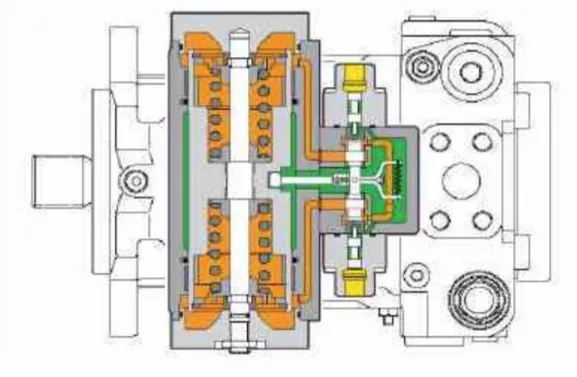
Overview of Hydraulic Control Systems These are control systems that utilize fluid power to transmit work from one point to another. A typical hydraulic system consists of reservoir, pumps, actuators, and valves. The pump is responsible for moving energy in form of a working fluid throughout the entire system while valves determine its rate and direction.The actuator then converts mechanical energy into pressure exerted by this particular liquid whereby it may facilitate several tasks depending upon need.
Hydraulic control systems are used across different industries like manufacturing, construction, agriculture, aerospace and defense among others due to their various advantages such as high power density; precise control; low noise levels.
Varieties of Hydraulic Compensation Valves
Hydraulic compensation valves are of different kinds, each for specific applications and operating conditions. This part explores some common types of hydraulic compensation valves.
Pressure Compensated Valves Pressure compensated valves keep a constant pressure level in a hydraulic system. They do this by using a pressure compensator to modulate the flow rate through the valve even if the demand in the system changes.
Flow Compensated Valves The function of flow compensated valves is regulate the speed at which hydraulic fluid passes through a system. These kinds of valves use flow compensators that change sizes of openings within them so as to control rates at which fluids move past them. They find their greatest application need where there is requirement for exact control over quantities moved like industrial machines or equipments used for production purposes.
Load Sensing Valves Load sensing valves vary amounts of hydraulic fluid that goes into or gets out from an actuator based on its load requirements. When applied with load-sensing compensators, these types adjust sizes of openings within themselves thereby controlling speeds at which fluids pass through them. They are widely employed in areas where loads applied onto systems fluctuate such as construction machinery vis-à-vis agricultural implements among others.
Directional Control Valve These are designed to direct flow directionality in hydraulic systems with multiple actuators working together towards achieving common objectives within one complete cycle time period; also referred to as DCVs because they can be used singly or stacked together (cascade) depending on complexity levels required during operation process under consideration here may include: cylinder strokes lengths travel distances involved per unit time duration etcetera – motors moving various parts simultaneously Example being excavator where boom up-down movement, arm in-out motion, bucket tilt back-forth action should all occur concurrently but sequentially too until desired result is achieved i.e complete digging cycle accomplished successfully hence requiring appropriate selection among other factors considered while designing such control schemes.
Proportional Control Valve Proportional control valves are designed with an in-built mechanism that allows for precise modulation of flow rates and pressures within a hydraulic system. They are fitted proportional solenoids which change sizes of openings within themselves leading to exactness in rates at which fluids move through them. These types find most application areas where high level accuracy is needed such as aerospace industry or defense establishments among others.
To sum up, there are many kinds of hydraulic compensator valves available that have been made for different uses under various conditions. Pressure compensated valves; flow compensated valves; load sensing valves; directional control valve(s); proportional control valve(s) – all these fall into category called ‘hydraulic compensation valve’. Thus, it is important to choose the right type depending on what one wants achieve from their system so as optimize performance levels while ensuring efficiency too.
Innovations in Hydraulic Compensation Valve Technology
Hydraulic compensation valves have seen significant improvements over time as people looked forward towards enhancing energy saving capabilities, system effectiveness and safety precautions. This section looks into some recent advancements made in this field of study;
Material Choice & Manufacturing Process: The advents achieved through materials science coupled with latest manufacturing techniques have resulted into new material properties characterized by enhanced toughness as well resistance against corrosion effects . For example; use ceramics within hydraulic compensators can significantly reduce wear rate thus prolonging useful life span for those devices .
Electrical Controls Systems Integration: With electronic controls systems being integrated alongside hydraulics based components like actuators or motors etcetera , better operational efficiencies may be realized since now it’s possible to precisely measure openings amount at which each fluid enters/exits particular actuator depending on its load need during certain instances . Electronic controls systems also enable remote monitoring plus maintenance activities hence facilitating real time performance analysis vis-à-vis appropriate action(s) taken when necessary .
Energy efficiency enhancements The growth of energy-saving hydraulic compensator valves is becoming more important today where sustainability matters most. Speed pumps which are variable and load-sensing valves among other innovations cut down the amount of power used by regulating flow rate and pressure in line with demand.
Safety features Safety is a major concern because hydraulic systems work under very high pressure conditions that could be dangerous. Technology improvements in compensatory valve design include safety features such as pressure relief (safety) valves for protecting against overpressure; check (non-return) valves to prevent backflow while ensuring correct system operation.
Minimization and modularization Progress in miniaturization and modularization has resulted into creation small size multipurpose hydraulic compensators applicable across wide areas. These allow better utilization of space within systems hence leading to increased efficiency in usage of resources.
In conclusion, the advancements made on hydraulic compensator valve technologies have led to improved performance, energy efficiency, and safety within the systems involved. Some recent trends in this area encompass electronic control systems; materials development as well as manufacturing techniques advancement among others such like energy saving measures themselves safety features or even compacting them into smaller sizes while still maintaining their capabilities besides making interchangeable units possible too that can serve different purposes at once wherever needed most hence catering for diverse needs which may arise from time-to-time when dealing with hydraulics since people want things done faster but also save power wherever necessary.
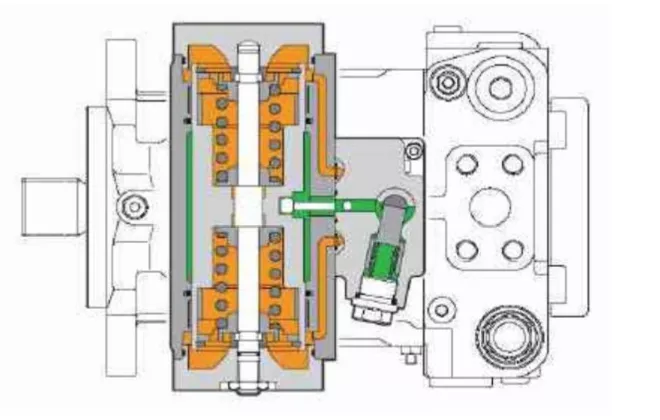
Applications of valve technology for hydraulic compensation
Hydraulic compensating valves have various applications in different industries where they aid in regulating the flow and pressure of fluids, controlling system motion as well as enhancing system performance. In this part, we will discuss some of the most common applications of hydraulic compensator valve technology.
Construction and heavy machinery Hydraulic compensator valves are extensively used in construction and heavy machinery to control the movement of hydraulic cylinders, motors among other components. These valves enable accurate control over the movement of bulky equipment which enhances efficiency and safety during operation.
Industrial machinery and manufacturing In industrial machinery and manufacturing, hydraulic compensator valves help regulate fluid flow and pressure, control system motion and improve system efficiency. Such valves find common use in injection molding, metal stamping as well as machine tooling where exact control over system operation is critical.
Agricultural equipment Hydraulic compensators also find use with agricultural equipment where they help in controlling the movement of hydraulic cylinders and motors besides regulating fluid flow and pressure. Common applications include crop harvesting; plowing among others that require precise system operation control.
Aerospace & Defense Aerospace systems heavily rely on hydraulic compensators which actuate hydraulics for guiding flight controls. They are critical components within these systems since they ensure safe travel through accurate modulation of forces applied by actuators onto aircraft surfaces during different stages (roll/pitch/yaw). Also used widely across landing gear systems like nose wheel steering etc., military aviation applications such as missile launchers or bomb racks need them too!
Marine & Offshore Marine vessels involve complex machines where power generation occurs using hydraulics even threadinchings operations can be done by rotating shafts mechanically connected via gearboxes then winches pull cables attached across deck equipements together while cranes lift heavy cargos onto shipboard areas so having appropriate types valving here becomes crucially important indeed!.
Predictive maintenance and condition monitoring The use of predictive maintenance and condition monitoring is gaining popularity in hydraulic control systems. By checking how the system is working and studying information, it can be made more efficient than ever before. This will help to identify and fix any potential problems before they cause the whole thing to stop functioning.
Integration with other technologies Hydraulic control systems are increasingly being combined with various other technologies like artificial intelligence, robotics or virtual reality among others. These combinations have led to creation of new uses that were unheard of previously such as automation in advanced manufacturing industry
Sustainability and environmental impact Energy saving hydraulic systems are being developed due to sustainability concerns and need for reduced environmental pollution. Variable speed pumps, load sensing valves or regenerative braking systems are some of the innovations introduced so far which help in lowering power consumption as well as minimizing ecological footprint.
In conclusion, what we can say is this – modern industrial needs necessitate changes in hydraulic control systems; these changes should seek for higher efficiency levels while at the same time trying to achieve increased productivity through automation processes coupled with care for environmental conservation aspects. Automation & remote control; smart & connected systems; predictive maintenance & condition monitoring; integration with other technologies; sustainability & environmental impact – these are just few among many possible future trends within this particular field of study (fluid power engineering).
Design and Development of Hydraulic Compensator Valves
Hydraulic compensator valves are a complex design and development process, which requires an understanding of hydraulic principles, materials science and manufacturing techniques. These steps will be elaborated in detail in this section.
Engineering design principles Designing hydraulic compensator valves begins with identifying system requirements such as desired flow rates, pressure ranges, and operating conditions. In the design process, selecting the right valve type, size, and material that can meet these criteria is important. Moreover, the valve must be able to endure stress levels and pressure from the hydraulic system.
Computational modeling and simulation Computational models are employed for improving designs for hydraulic compensator valves. This entails developing computer models of the valve that can simulate its working under diverse operational environments. The output of these simulations is used to refine the valve’s design so as it can correspond to the proposed performance specifications.
Prototype development and testing Once perfected, a prototype for a hydraulic compensator valve is made to test whether it works properly under different operating circumstances. Normally this prototype will be tested using a hydraulic test rig which mimics operating conditions within a hydraulic system. This phase identifies any problems or deficiencies in valve design.
Performance optimization and improvement The final stage in designing and developing a product is performance optimization which entails identifying areas for improvement of the hydraulic compensator valve design. In order to enhance its performance there might be need to make changes to various aspects of the valve designs For instance this could mean reducing response time or making it more durable with extended life expectancy.
In conclusion, thorough understanding on Hydraulic Principles Material Science & Manufacturing Techniques required when designing & Developing Hydraulic Compensatory Valve(s). The processes involved include engineering design principles computational modeling & simulation prototype development & testing; Performance Optimization & Improvement . Thus proper functioning of systems calls for good designing of Hydraulic Compensation Valves (HCVs).
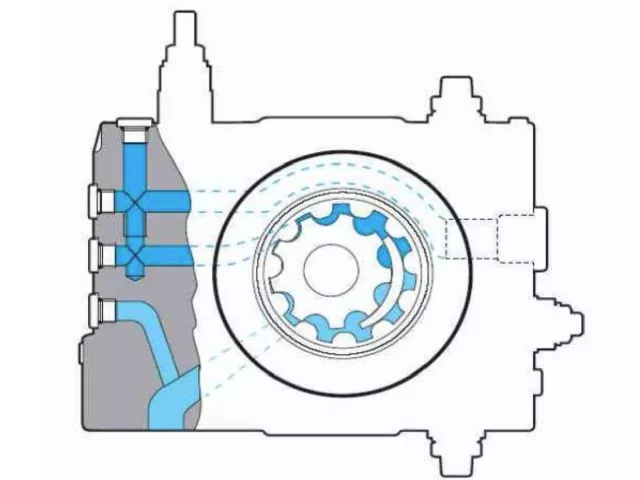
Maintenance and Troubleshooting of Hydraulic Compensator Valves
For optimum system performance and prevention of expensive downtimes, it is imperative to properly maintain and troubleshoot hydraulic compensator valves. These will be discussed in this section.
Routine maintenance procedures Hydraulic compensator valves need to be cleaned inspected and lubricated at regular intervals as part of routine maintenance practices. The frequency of such procedures can vary depending on the operating conditions within a hydraulic system; nevertheless, valves should generally be checked as well as serviced at least once a year.
Troubleshooting common issues Common troubles that occur with the hydraulic compensator valve are leaks, blockages and valve failures. Troubleshooting these problems requires finding out the cause like examining valve components or monitoring flow rate/pressure via system data analysis.
Diagnosis and repair techniques Fixing hydraulic compensator valves normally entails disassembling them so that the parts can be examined and replaced if damaged or worn out. While diagnosing & repairing hydraulic valves it is very important that one sticks to guidelines from manufacturers so as to make sure they are correctly reassembled & calibrated accordingly.
Best practices for hydraulic compensator valve longevity
To prolong the lifespan of hydraulic compensator valves, it is required that they be serviced regularly, installed properly and used within their specified operational limits. Additionally, one should ensure that the correct fluid is used and it does not contain any contaminants which over time can destroy the components.
In conclusion, proper maintenance and troubleshooting of hydraulic compensator valves are critical to ensure optimal system performance and prevent costly downtime. When working with hydraulic compensator valves, routine maintenance procedures, troubleshooting common issues, diagnosis and repair techniques as well as best practices for prolonging valve lifespan are all important considerations in this regard. Adherence to these guidelines will help ensure efficient and reliable operation of hydraulic systems throughout their life spans.
Market Analysis and Industry Landscape
The market for hydraulic compensator seals has become dynamic and fast growing because of its efficiency in terms of speed, reliability and being eco-friendly among others. The following sections explore on the market analysis and industry landscape concerning Hydraulic Compensator Valves.
Market size and growth projections According to Market Research Future’s report, global hydraulic valve market is expected to grow at a CAGR of 4.2% from 2017 to 2023. This growth is driven by major industries such as construction industry among others.
Key players & Market competition Some key players competing for market share in the Hydraulic Compensator Valve Market include Bosch Rexroth, Parker Hannifin Corporation (U.S.), Eaton Corporation Plc (Ireland), Danfoss Power Solutions ApS (Denmark), Kawasaki Heavy Industries Ltd.(Japan) amongst others.
Emerging market trends & Opportunities Several emerging trends can be identified within the Hydraulic Compensators Valve Market including demand for energy-efficient/sustainable technologies; integration with other technologies such as robotics/AI; automation/remote control developments in hydraulics among others. These trends present significant opportunities for companies that can innovate and stay ahead of the curve.
Regulatory landscape & Standards Compliance The hydraulic compensator valve market is subject to various regulatory standards and compliance requirements, such as ISO 9001, ISO 14001 and OHSAS 18001. This ensures that hydraulic systems operate safely, efficiently and sustainably.
Moving forward, the market for hydraulic compensators has become dynamic and fast growing because it is eco-friendly as well as efficient in terms of speed among others. Market size and growth projections, key players & market competition, emerging market trends & opportunities as well as regulatory landscape & standards compliance are all important considerations for companies operating in this industry. There is thus likelihood of further innovation within the hydraulic compensator valve Market due to the increasing demand for more efficient and sustainable Hydraulic systems.